Dual-face locking knife handle-spindle system joint part stiffness characteristic optimization method based on particle swarm optimization
A technology of particle swarm algorithm and stiffness characteristics, which is applied in the field of toolholder-spindle system dynamic characteristics analysis, can solve problems such as the separation of conical joint surfaces, affecting the dynamic performance of the system, and reducing the stiffness of the joint
- Summary
- Abstract
- Description
- Claims
- Application Information
AI Technical Summary
Problems solved by technology
Method used
Image
Examples
Embodiment Construction
[0014] The following is attached Figure 1-3 The present invention is described in further detail.
[0015] Step (1) Establish a three-dimensional normal and tangential stiffness model, and write a MATLAB program; establish a double-sided locking tool holder-spindle system joint torsional and radial stiffness model, and write a MATLAB program.
[0016] Based on the M-B fractal theory, combined with the Hertz theory, and considering the elastoplastic deformation and domain expansion factor ψ, the total elastic normal load, elastoplastic normal load and The total plastic normal loads are as follows:
[0017]
[0018]
[0019]
[0020] where H G1 ,H G2 Both are coefficients related to material properties and fractal parameters of the joint surface,
[0021] H is the hardness of the softer material, H=2.8Y (Y is the yield strength value); k is a parameter related to Poisson's ratio, k=0.454+0.41ν; a' 1c ,a' 2c are the critical cross-sectional areas between elastic...
PUM
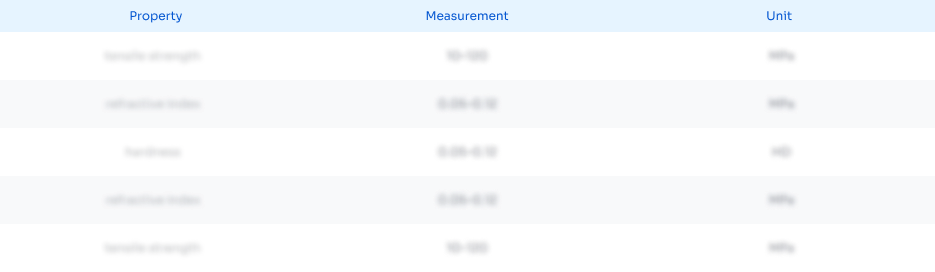
Abstract
Description
Claims
Application Information

- Generate Ideas
- Intellectual Property
- Life Sciences
- Materials
- Tech Scout
- Unparalleled Data Quality
- Higher Quality Content
- 60% Fewer Hallucinations
Browse by: Latest US Patents, China's latest patents, Technical Efficacy Thesaurus, Application Domain, Technology Topic, Popular Technical Reports.
© 2025 PatSnap. All rights reserved.Legal|Privacy policy|Modern Slavery Act Transparency Statement|Sitemap|About US| Contact US: help@patsnap.com