Manufacturing method for automobile lamp light source
A manufacturing method and light source technology, applied in the field of car lamp manufacturing, to achieve the effect of high light output and convenient and quick installation
- Summary
- Abstract
- Description
- Claims
- Application Information
AI Technical Summary
Problems solved by technology
Method used
Image
Examples
Embodiment Construction
[0024] The present invention will be further described below in conjunction with the accompanying drawings of the description.
[0025] A method for manufacturing a car light source, comprising the steps of making a heat sink, the step of making an LED lamp board, and the steps of cooperating between the LED lamp board and the heat sink.
[0026] In the manufacturing step of the heat sink, such as figure 1 , 2 As shown, the heat sink 1 is formed by stretching, and the inside of the heat sink 1 is a hollow structure to form a cavity 11 , a PCB board can be arranged in the cavity 11 , and one end of the PCB board is connected to the lamp head arranged at one end of the heat sink 1 . The cavity 11 can also form a heat dissipation air duct to take away the heat from the heat dissipation seat 1 and the PCB board, so as to reduce the temperature. The heat sink 1 is roughly a hexagonal cylinder. When installed, the heat sink 1 is set horizontally. Its top and bottom surfaces are bo...
PUM
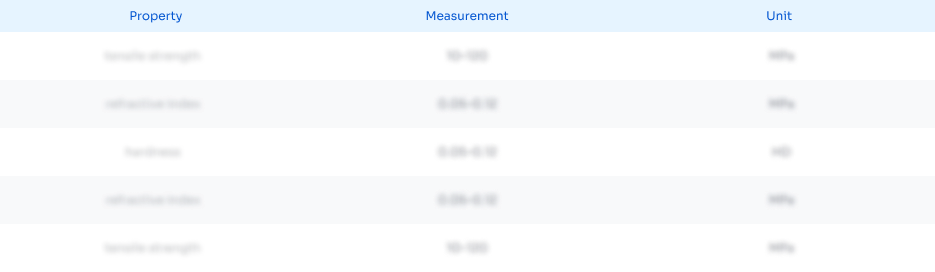
Abstract
Description
Claims
Application Information

- Generate Ideas
- Intellectual Property
- Life Sciences
- Materials
- Tech Scout
- Unparalleled Data Quality
- Higher Quality Content
- 60% Fewer Hallucinations
Browse by: Latest US Patents, China's latest patents, Technical Efficacy Thesaurus, Application Domain, Technology Topic, Popular Technical Reports.
© 2025 PatSnap. All rights reserved.Legal|Privacy policy|Modern Slavery Act Transparency Statement|Sitemap|About US| Contact US: help@patsnap.com