Space truss and spaceflight loading structure for space operation
A space truss, aerospace technology, applied in the direction of non-rotational vibration suppression, etc., can solve the problems of decreased precision of optoelectronic instruments, deformation of structural parts, circuit short circuit, etc., to facilitate assembly, launch and transportation, meet the needs of space operations, and improve vibration reduction. performance effect
- Summary
- Abstract
- Description
- Claims
- Application Information
AI Technical Summary
Problems solved by technology
Method used
Image
Examples
Embodiment
[0035] The structural design of the space truss can better play a vibration damping effect, thereby realizing the vibration damping effect on the box structure 1 . The first long pipe 10 and the second long pipe 11 are tubular members, which are hollow pipes with a wall thickness of 2 mm. By applying a free damping layer 7 on the connecting pipe 6, the free damping layer 7 is connected with the first long pipe 10 and the second long pipe. The two long pipes 11 are connected by adhesive. The thickness, application position and application area of the free damping layer 7 can be changed by changing the diameter and length of the connecting pipe 6 . Each surface of the connecting block 4 is provided with a threaded hole, and the threaded hole is connected with the connecting piece 5. This structure has space ductility and can be easily expanded and installed. On multiple connecting blocks 4, except for tooling 9. On the eight surfaces in contact with the box structure 1, there...
PUM
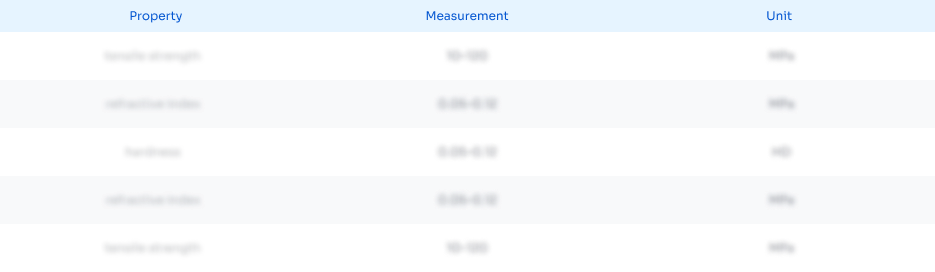
Abstract
Description
Claims
Application Information

- Generate Ideas
- Intellectual Property
- Life Sciences
- Materials
- Tech Scout
- Unparalleled Data Quality
- Higher Quality Content
- 60% Fewer Hallucinations
Browse by: Latest US Patents, China's latest patents, Technical Efficacy Thesaurus, Application Domain, Technology Topic, Popular Technical Reports.
© 2025 PatSnap. All rights reserved.Legal|Privacy policy|Modern Slavery Act Transparency Statement|Sitemap|About US| Contact US: help@patsnap.com