Polyester cotton dispersing and reactive dye one bath process dyeing technology
A technology of reactive dyes and disperse dyes, applied in the field of dyeing, can solve the problems of COD load, excessive color floating, sewage discharge, etc., and achieve the effects of improving equipment utilization, full color, and improving worker productivity
- Summary
- Abstract
- Description
- Claims
- Application Information
AI Technical Summary
Problems solved by technology
Method used
Image
Examples
Embodiment 1
[0018] In this embodiment, a polyester-cotton disperse and reactive dye one-bath dyeing process includes: preparing a dye solution at room temperature, adjusting the pH of the dye solution to 5, immersing the polyester-cotton at a bath ratio of 1:20, and using a temperature of 1.5° C. / min. Raise the temperature to 50°C, keep it for 10 minutes, then raise the temperature to 140°C at a rate of 3.5°C / min, keep it for 40 minutes, isolate the rare earth complexed microencapsulated disperse dye for 20 minutes, and cool down to 80°C at a rate of 1.5°C / min , initial washing, soaping, final washing, drying;
[0019] Wherein, the dyeing solution includes: reactive dye 2% owf, rare earth complex microencapsulated disperse dye 3.5% owf, Yuanming powder 10g / L, pH buffer 2.5g / L, organic phenol halide 0.2g / L, Organic fluorine surfactant 0.03g / L.
Embodiment 2
[0021] In this embodiment, a polyester-cotton disperse and reactive dye one-bath dyeing process includes: preparing a dye solution at room temperature, adjusting the pH of the dye solution to 4, immersing the polyester-cotton at a bath ratio of 1:30, and using a temperature of 1° C. / min. Raise the temperature to 55°C, keep it warm for 8 minutes, then raise the temperature to 135°C at a rate of 4°C / min, keep it warm for 45 minutes, isolate the disperse dye microcapsules and continue dyeing for 15 minutes, cool down to 75°C at a rate of 2°C / min, at 25°C After washing with water for 5 minutes, soap at 95°C for 10 minutes, and the soaping agent used includes: NP-10 5g / L, soda ash 1g / L, then wash with water at 50°C for 5 minutes, and dry;
[0022] Wherein, the dyeing solution includes: reactive dye 3% owf, rare earth complex microencapsulated disperse dye 2% owf, sodium sulfate 15g / L, pH buffer 1.5g / L, 2,4,6-trichlorophenol 0.3g / L, organic fluorine surfactant 0.01g / L;
[0023] The...
Embodiment 3
[0025] In this embodiment, a polyester-cotton disperse and reactive dye one-bath dyeing process includes: preparing a dye solution at room temperature, adjusting the pH of the dye solution to 6, immersing the polyester-cotton at a bath ratio of 1:10, and using a temperature of 2°C / min. Raise the temperature to 45°C, keep it warm for 12 minutes, then raise the temperature to 145°C at a rate of 3°C / min, keep it warm for 35 minutes, isolate the rare earth complexed microencapsulated disperse dye for 25 minutes, and cool down to 85°C at a rate of 1°C / min , after washing at 15°C for 15 minutes, soaping at 85°C for 25 minutes, and the soaping agent used includes: NP-10 1g / L, soda ash 2g / L, then washing at 40°C for 20 minutes, and drying;
[0026] Wherein, the dyeing solution includes: 1% owf of reactive dyes, 5% owf of rare earth complexed microencapsulated disperse dyes, 5 g / L of sodium sulfate, 3.5 g / L of pH buffer, 2,4,5-trichlorophenol 0.1g / L, organic fluorine surfactant 0.05g / L...
PUM
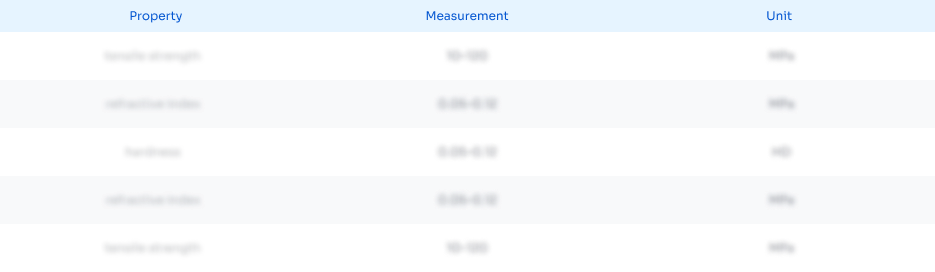
Abstract
Description
Claims
Application Information

- R&D
- Intellectual Property
- Life Sciences
- Materials
- Tech Scout
- Unparalleled Data Quality
- Higher Quality Content
- 60% Fewer Hallucinations
Browse by: Latest US Patents, China's latest patents, Technical Efficacy Thesaurus, Application Domain, Technology Topic, Popular Technical Reports.
© 2025 PatSnap. All rights reserved.Legal|Privacy policy|Modern Slavery Act Transparency Statement|Sitemap|About US| Contact US: help@patsnap.com