Manufacturing method of high-strength durable duplex printing grid material
A manufacturing method and durable technology, applied in textiles and papermaking, etc., can solve problems such as waste of resources, achieve the effects of reducing coloring, good low temperature resistance, and preventing performance decline
- Summary
- Abstract
- Description
- Claims
- Application Information
AI Technical Summary
Problems solved by technology
Method used
Examples
Embodiment 1
[0030] 1) The following weight components are mixed into impregnating agent:
[0031] PVC paste resin 100 parts
[0032] 65 parts plasticizer
[0033] Stabilizer 3 parts
[0034] Carbon black 2 parts
[0035] 2) Filter the mixed impregnating agent, and use 80-mesh nylon mesh for filtration;
[0036] 3) Pass the 1000D*1000D polyester woven fabric with a density of 8*8 strands / cm through the layer machine at a uniform speed through the unwinding mechanism, and add 1.8 kg of cross-linking agent per 100 kg of impregnating agent, and the isocyanate group in the cross-linking agent (- The content of NCO) is 3%, the coating amount is 105g / m2, evenly coated on the polyester woven fabric, and dried in an oven at a temperature of 140°C;
[0037] 4) After being plasticized and formed in an oven, it is used for surface treatment. The temperature during plasticization is 200 ° C, embossed, and the finished product is obtained.
Embodiment 2
[0039] 1) The following weight components are mixed into impregnating agent:
[0040] PVC paste resin 100 parts
[0041] Plasticizer 100 parts
[0042] Stabilizer 5 parts
[0043] 2) Grinding and filtering the mixed impregnating agent, and selecting 80 mesh nylon mesh for filtering;
[0044] 3) The polyester woven fabric with a density of 1000D*1000D of 8*8 strands / cm passes through the coating machine at a uniform speed through the unwinding mechanism, and 5 kg of crosslinking agent is added to every 100kg of layer agent, and the isocyanate group in the crosslinking agent ( -NCO) content is 5%, the coating amount is 350g / m2, evenly coated on the polyester woven fabric, dried in an oven at 200°C, and then coated with a layer of impregnating agent, and Do drying.
[0045] 4) After being plasticized and formed in an oven, it is used for surface treatment. The temperature during plasticization is 210°C, embossed, and the finished product is obtained.
Embodiment 3
[0047] 1) The following weight components are mixed into impregnating agent:
[0048] PVC paste resin 100 parts
[0049] Plasticizer 50 parts
[0050] Stabilizer 1 part
[0051] 1 part medium chrome yellow
[0052] 2) Grinding and filtering the mixed impregnating agent, and selecting 80 mesh nylon mesh for filtering;
[0053] 3) Pass the 1000D*1000D polyester woven fabric with a density of 8*8 strands / cm through the coating machine at a uniform speed through the unwinding mechanism, and add 1kg of crosslinking agent to every 100kg of impregnating agent, and the isocyanate group in the crosslinking agent (- The content of NCO) is 4%, and the coating amount is 100g / m2, evenly coated on the polyester woven fabric, and dried in an oven at a temperature of 160 °C, and then coated with a layer of impregnating agent, and carried out Drying process.
[0054] 4) After being plasticized and formed in an oven, it is used for surface treatment. The temperature during plasticization i...
PUM
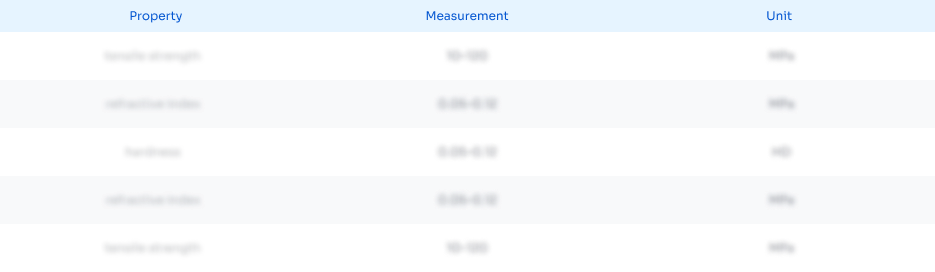
Abstract
Description
Claims
Application Information

- Generate Ideas
- Intellectual Property
- Life Sciences
- Materials
- Tech Scout
- Unparalleled Data Quality
- Higher Quality Content
- 60% Fewer Hallucinations
Browse by: Latest US Patents, China's latest patents, Technical Efficacy Thesaurus, Application Domain, Technology Topic, Popular Technical Reports.
© 2025 PatSnap. All rights reserved.Legal|Privacy policy|Modern Slavery Act Transparency Statement|Sitemap|About US| Contact US: help@patsnap.com