Method for partially recycling anaerobic digestion solution to serve as mixing water for alcohol production
A production method, anaerobic digestion technology, applied in the direction of biofuel, waste fuel, fermentation, etc., can solve the problems of increasing cost, using chemicals, affecting the reuse effect of anaerobic digestion liquid, etc., to reduce alkalinity and avoid inhibition , The effect of exempting equipment investment
- Summary
- Abstract
- Description
- Claims
- Application Information
AI Technical Summary
Problems solved by technology
Method used
Image
Examples
Embodiment 1
[0024] The present invention adopts the following process steps in a process of using anaerobic digestion effluent as part of the mixing water for alcohol fermentation:
[0025] Mix cassava flour with the previous batch of anaerobic digestion effluent clear liquid and tap water, the ratio of material to water is 1:3, the proportion of anaerobic digestion effluent to the total mixing water is 50% (v / v), add high temperature resistant α-starch Enzyme (10U / g starch), stir well, heat to 90°C and maintain for 100min; cool down to 60°C, add glucoamylase (180U / g starch), stir well, keep warm for saccharification for 30min. After the saccharification was completed, the temperature was lowered to 30° C., and 15% (v / v) yeast seed solution was inserted to start fermentation, and the fermentation time was 42 hours. After fermentation, alcohol and distiller's grain wastewater are obtained through distillation and rectification. The distiller's grains are centrifuged to obtain the distille...
Embodiment 2
[0029] The present invention uses the following process steps in a process of using anaerobic digestion effluent as part of the mixing water for alcohol fermentation:
[0030]The corn flour was mixed with the previous batch of anaerobic digestion effluent clear liquid and fresh surface water, the ratio of material to water was 1:2.2, and the proportion of anaerobic digestion effluent to the total mixing water was 35% (v / v). Add high-temperature-resistant α-amylase (15U / g starch), stir well, heat to 95°C and maintain for 120min; cool down to 60°C, add glucoamylase (200U / g starch), stir well, and keep warm for saccharification for 15min. After saccharification, the temperature was lowered to 30° C., and 20% (v / v) yeast seed solution was inserted to start fermentation, and the fermentation time was 52 hours. After fermentation, alcohol and distiller's grain wastewater are obtained through distillation and rectification. The distiller's grains are centrifuged to obtain the distil...
Embodiment 3
[0035] The present invention adopts the following process steps in a process of using anaerobic digestion effluent as part of the mixing water for alcohol fermentation:
[0036] Mix cassava flour, wheat flour and corn flour with the last batch of anaerobic digestion effluent, tap water and tank washing water, the ratio of material to water is 1:3, and the proportion of anaerobic digestion effluent to the total mixing water is 10% (v / v) . Add high-temperature resistant α-amylase (10U / g starch), stir well, heat to 90°C and maintain for 100min; cool down to 59°C, add glucoamylase (180U / g starch), stir well, then cool to 30°C, saccharification time 0 min, insert 15% (v / v) yeast seed solution to start fermentation, and the fermentation time is 42 hours. After fermentation, alcohol and distiller's grain wastewater are obtained through distillation and rectification. The distiller's grains are centrifuged to obtain the distiller's grains clear liquid, and the distiller's grains cle...
PUM
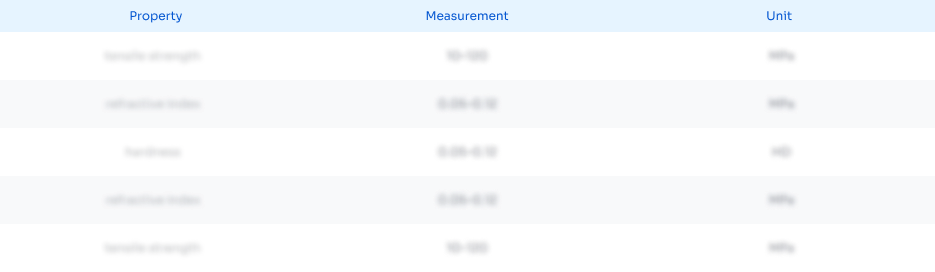
Abstract
Description
Claims
Application Information

- R&D Engineer
- R&D Manager
- IP Professional
- Industry Leading Data Capabilities
- Powerful AI technology
- Patent DNA Extraction
Browse by: Latest US Patents, China's latest patents, Technical Efficacy Thesaurus, Application Domain, Technology Topic, Popular Technical Reports.
© 2024 PatSnap. All rights reserved.Legal|Privacy policy|Modern Slavery Act Transparency Statement|Sitemap|About US| Contact US: help@patsnap.com