Preparation method of scratch-resistant high-impact-resistance PMMA (polymethyl methacrylate) material
A high-impact and scratch-resistant technology, which is applied in the preparation of high-impact PMMA materials and in the field of scratch resistance, can solve the problems of low surface hardness and low impact resistance of PMMA, and achieve a stable and controllable reaction system. The effect of easy operation and simple preparation method
- Summary
- Abstract
- Description
- Claims
- Application Information
AI Technical Summary
Problems solved by technology
Method used
Image
Examples
Embodiment 1
[0013] Weigh 80 parts of main monomer MMA, 5 parts of butyl acrylate, 15 parts of styrene, initiator 15×10 parts by weight -4 0.2 parts of chain transfer agent, placed in a three-necked flask equipped with a reflux condensing device, a thermometer, and a stirring rod, and stirred evenly, heated in an oil bath to 110°C, and the stirring speed was 350r / min. As the reaction progressed, the viscosity of the system gradually Increase, when the reaction time is 4h50min, increase the stirring speed to 450r / min, continue the constant temperature reaction for 3h40min, and form a viscous copolymerization product; stop the reaction, take out the copolymerization product after the system is cooled, dissolve it completely with acetone, and then settle it with methanol The copolymer was taken out, filtered, and dried in an oven at a drying temperature of 100° C. for 3 hours to obtain a methyl methacrylate-butyl acrylate-styrene copolymer.
Embodiment 2
[0015] Weigh 70 parts of main monomer MMA, 10 parts of butyl acrylate, 15 parts of styrene, initiator 25×10 parts by weight -4 0.2 parts of chain transfer agent, placed in a three-necked flask equipped with a reflux condensing device, a thermometer, and a stirring rod, and stirred evenly, heated in an oil bath to 108°C, and the stirring speed was 350r / min. As the reaction progressed, the viscosity of the system gradually Increase, when the reaction time is 3h20min, increase the stirring speed to 450r / min, continue the constant temperature reaction for 3h20min, and form a viscous copolymerization product; stop the reaction, take out the copolymerization product after the system is cooled, dissolve it completely with acetone, and then settle it with methanol The copolymer was taken out, filtered, and dried in an oven at a drying temperature of 100° C. for 3 hours to obtain a methyl methacrylate-butyl acrylate-styrene copolymer.
Embodiment 3
[0017] Weigh 100 parts of main monomer MMA, 10 parts of butyl acrylate, 5 parts of styrene, initiator 35×10 parts by weight -4 0.3 parts of chain transfer agent, placed in a three-necked flask equipped with a reflux condensing device, a thermometer, and a stirring rod, and stirred evenly, heated in an oil bath to 112°C, and the stirring speed was 500r / min. As the reaction progressed, the viscosity of the system gradually Increase, when the reaction time is 3h20min, increase the stirring speed to 450r / min, continue the constant temperature reaction for 3h20min, and form a viscous copolymerization product; stop the reaction, take out the copolymerization product after the system is cooled, dissolve it completely with acetone, and then settle it with methanol The copolymer was taken out, filtered, and dried in an oven at a drying temperature of 60° C. for 8 hours to obtain a methyl methacrylate-butyl acrylate-styrene copolymer.
PUM
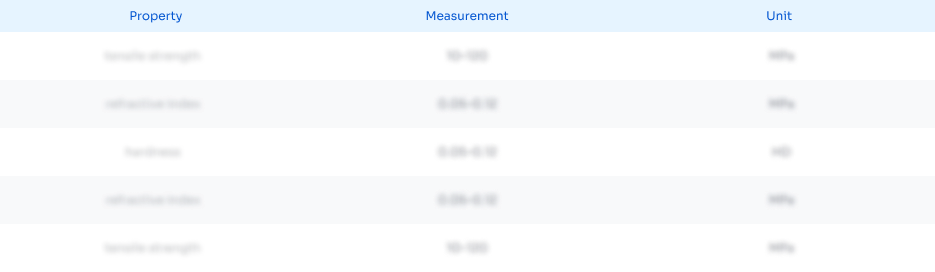
Abstract
Description
Claims
Application Information

- R&D Engineer
- R&D Manager
- IP Professional
- Industry Leading Data Capabilities
- Powerful AI technology
- Patent DNA Extraction
Browse by: Latest US Patents, China's latest patents, Technical Efficacy Thesaurus, Application Domain, Technology Topic, Popular Technical Reports.
© 2024 PatSnap. All rights reserved.Legal|Privacy policy|Modern Slavery Act Transparency Statement|Sitemap|About US| Contact US: help@patsnap.com