Pressure casting device and method
A mold base and exhaust channel technology, applied in the field of die-casting, can solve problems affecting the quality of die-casting parts, long die-casting time, and low production efficiency, and achieve the effect of promoting the solidification of liquid metal, reducing porosity, and improving production efficiency
- Summary
- Abstract
- Description
- Claims
- Application Information
AI Technical Summary
Problems solved by technology
Method used
Image
Examples
Embodiment Construction
[0035] In order to make the object, technical solution and advantages of the present invention clearer, the present invention will be further described in detail below in conjunction with the embodiments. It should be understood that the specific embodiments described here are only used to explain the present invention, not to limit the present invention.
[0036] figure 1 It is a schematic diagram of a die-casting device according to the present invention. As shown in the figure, the die casting device generally includes a mold 100 , an exhaust structure 200 and a vacuum pump 300 . Wherein, mold 100 comprises first mold base 110, second mold base 120 and when first mold base 110 and second mold base 120 are closed by first mold base 110 and mold cavity 130 defined by second mold base 120 and pouring. Mouth 140. The cavity 130 can be made into any shape according to specific requirements, and the gate 140 communicates the cavity 130 with the outside of the mold 100 for pour...
PUM
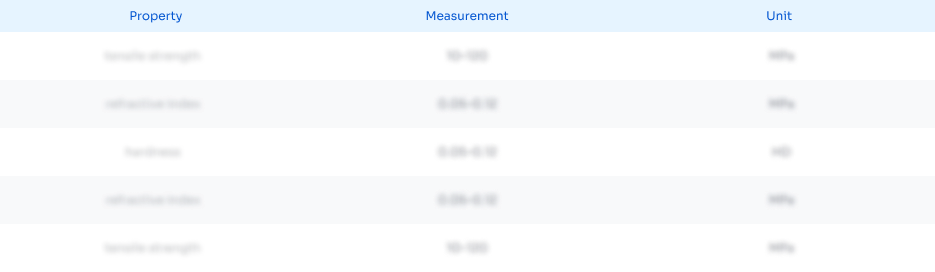
Abstract
Description
Claims
Application Information

- R&D
- Intellectual Property
- Life Sciences
- Materials
- Tech Scout
- Unparalleled Data Quality
- Higher Quality Content
- 60% Fewer Hallucinations
Browse by: Latest US Patents, China's latest patents, Technical Efficacy Thesaurus, Application Domain, Technology Topic, Popular Technical Reports.
© 2025 PatSnap. All rights reserved.Legal|Privacy policy|Modern Slavery Act Transparency Statement|Sitemap|About US| Contact US: help@patsnap.com