A kind of flaky carbonyl functionalized carbon material and its preparation method and application
A functionalized, carbon material technology, applied in the manufacture of hybrid/electric double-layer capacitors, electrodes of hybrid capacitors, etc., can solve the problems of poor capacitance performance, poor application, and unenvironmental protection, achieving low cost, simple operation, Excellent energy storage performance
- Summary
- Abstract
- Description
- Claims
- Application Information
AI Technical Summary
Problems solved by technology
Method used
Image
Examples
Embodiment 1
[0037] 0.94g of phenol was dissolved in 20ml of water to obtain a precursor solution with a concentration of 0.5mol / L, and then 2.5ml of formaldehyde (37%) was added to the precursor solution and mixed uniformly to obtain a mixed precursor solution. The prepared mixed precursor solution was impregnated onto calcium hydroxide by incipient wetness impregnation and kept for 72 hours to obtain a mixture of oligomeric resin / calcium hydroxide, and the mixture of oligomeric resin / calcium hydroxide was thermoset at 120°C After 48 hours a cured resin / calcium hydroxide mixture was obtained. The obtained cured resin / calcium hydroxide mixture was roasted in an argon atmosphere at 600°C for 4 hours to obtain a carbon / calcium oxide composite structure, and the carbon / calcium oxide composite structure was placed in 100ml of hydrochloric acid with a concentration of 0.2mol / L Carrying out etching to remove calcium oxide, then carrying out suction filtration, washing and drying to obtain a thin...
Embodiment 2
[0039]1.11 g of catechol was dissolved in 10.0 ml of water to obtain a precursor solution with a concentration of 1.0 mol / L, and then 2.5 ml of formaldehyde (37%) was added to the precursor solution and mixed uniformly to obtain a mixed precursor solution. The prepared mixed precursor solution was impregnated onto magnesium hydroxide by incipient wetness impregnation and kept for 48 hours to obtain a mixture of oligomeric resin / magnesium hydroxide, and the mixture of oligomeric resin / magnesium hydroxide was thermoset at 100°C After 24 h a cured resin / magnesium hydroxide mixture was obtained. The obtained cured resin / magnesium hydroxide mixture was roasted in an argon atmosphere at 700°C for 2 hours to obtain a carbon / magnesia composite structure, and the carbon / magnesia composite structure was placed in 100ml of hydrochloric acid with a concentration of 0.2mol / L Carry out etching to remove magnesia, then perform suction filtration, wash and dry to obtain a thin sheet-shaped ca...
Embodiment 3
[0041] 1.26g of trisphenol was dissolved in 5.0ml of water to obtain a precursor solution with a concentration of 2.0mol / L, and then 2.5ml of formaldehyde (37%) was added to the precursor solution and mixed uniformly to obtain a mixed precursor solution. The prepared mixed precursor solution was impregnated onto magnesium hydroxide by incipient wetness impregnation and kept for 24 hours to obtain a mixture of oligomeric resin / magnesium hydroxide, and the mixture of oligomeric resin / magnesium hydroxide was thermoset at 80°C After 12 h a cured resin / magnesium hydroxide mixture was obtained. The obtained cured resin / magnesium hydroxide mixture was roasted in an argon atmosphere at 800°C for 1 hour to obtain a carbon / magnesia composite structure, and the carbon / magnesia composite structure was placed in 100ml of hydrochloric acid with a concentration of 0.2mol / L Carry out etching to remove magnesia, then perform suction filtration, wash and dry to obtain a thin sheet-shaped carbon...
PUM
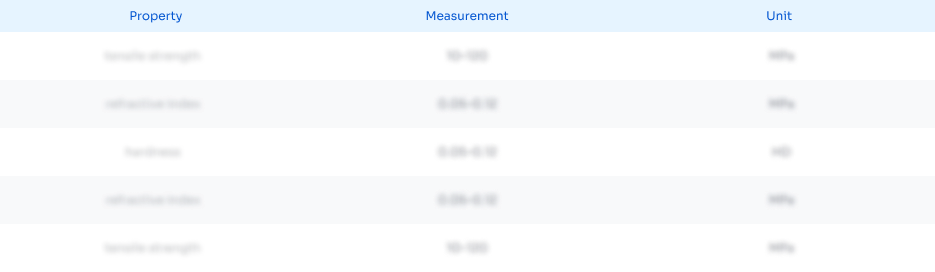
Abstract
Description
Claims
Application Information

- R&D Engineer
- R&D Manager
- IP Professional
- Industry Leading Data Capabilities
- Powerful AI technology
- Patent DNA Extraction
Browse by: Latest US Patents, China's latest patents, Technical Efficacy Thesaurus, Application Domain, Technology Topic, Popular Technical Reports.
© 2024 PatSnap. All rights reserved.Legal|Privacy policy|Modern Slavery Act Transparency Statement|Sitemap|About US| Contact US: help@patsnap.com