Preparation method of bent LED lamp filament and bulb provided with same
A LED filament and bending technology, which is applied in lighting and heating equipment, components of lighting devices, semiconductor devices of light-emitting elements, etc., can solve the problems of manufacturing process limitations, wattage limitations, difficulties, etc., and achieve uniform luminescence and long service life Long, high yield effect
- Summary
- Abstract
- Description
- Claims
- Application Information
AI Technical Summary
Problems solved by technology
Method used
Image
Examples
Embodiment Construction
[0033] The present invention will be described in further detail below in conjunction with the accompanying drawings and specific embodiments.
[0034] Depend on figure 1 It can be seen that the present invention first discloses a method for preparing a curved LED filament, which mainly includes the following steps:
[0035] (1) First prepare a number of metal substrates or non-metal substrates with good ductility, and make series or series-parallel conductive lines on the metal or non-metal substrates; metal substrates with good ductility such as aluminum substrates, copper substrates, copper substrates, Aluminum composite substrates, etc., non-metallic substrates such as composite plastic substrates, rubber substrates, silica gel substrates, etc., mainly adopt aluminum substrate 1 as an example in this embodiment (see figure 2 );
[0036] (2) Use a machine to punch or cut out a mosquito-repellent-repellent-repellent spiral structure on a metal or non-metallic substrate. ...
PUM
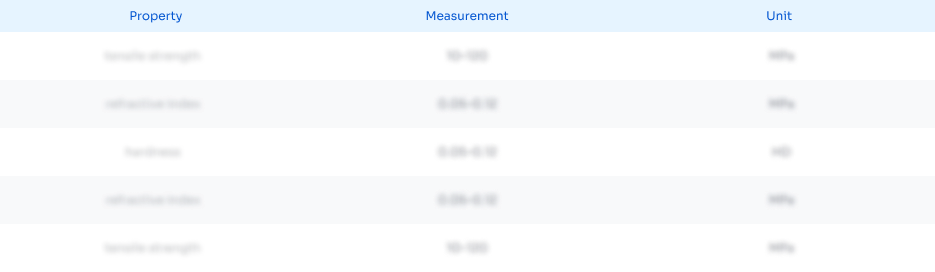
Abstract
Description
Claims
Application Information

- R&D Engineer
- R&D Manager
- IP Professional
- Industry Leading Data Capabilities
- Powerful AI technology
- Patent DNA Extraction
Browse by: Latest US Patents, China's latest patents, Technical Efficacy Thesaurus, Application Domain, Technology Topic, Popular Technical Reports.
© 2024 PatSnap. All rights reserved.Legal|Privacy policy|Modern Slavery Act Transparency Statement|Sitemap|About US| Contact US: help@patsnap.com