Groove machining method
A processing method and groove technology, applied in metal processing equipment, metal processing machinery parts, manufacturing tools, etc., can solve problems such as poor processing, increased power of movable tools, and increased frequency of blade confirmation, so as to increase the machining allowance, The effect of suppressing vibration
- Summary
- Abstract
- Description
- Claims
- Application Information
AI Technical Summary
Problems solved by technology
Method used
Image
Examples
no. 1 Embodiment
[0092] 4 is a schematic diagram showing a first embodiment of the method of processing a groove portion of the present invention using a single-cutting-edge type rotary tool, Figure 4A It is a diagram in which the relationship between the workpiece and the rotating tool is viewed from above with respect to the workpiece, Figure 4B It is viewed from the rear of the processing direction Figure 4A diagram of the relationship.
[0093] In addition, FIG. 5 is a schematic diagram showing a first embodiment of the groove portion processing method of the present invention using a double-sided cutting edge type rotary tool, Figure 5A It is a diagram in which the relationship between the workpiece and the rotating tool is viewed from above with respect to the workpiece, Figure 5B It is viewed from the rear of the processing direction Figure 5A diagram of the relationship.
[0094] In addition, in Fig. 4 and Fig. 5, all are the same as the case of Fig. 1 and Fig. 2, with respec...
no. 2 Embodiment
[0159] Next, a method of processing a groove portion according to a second embodiment of the present invention will be described with reference to FIG. 8 . Here, as an application example of the method of machining the groove portion, a case where a groove portion constituting a part of the gear shape is formed in a workpiece will be described.
[0160] 8 is a cross-sectional view showing an example of a processing sequence when a groove portion is formed by applying a groove portion processing method according to a second embodiment of the present invention, Figure 8A shows the general situation when the groove portion is processed to the first depth, Figure 8B shows the general situation when the groove is processed to the second depth, Figure 8C Shows the general situation when the groove is machined to the target machining depth, Figure 8D The general situation when the side surface and the bottom surface of the groove portion are processed is shown.
[0161] Here, ...
PUM
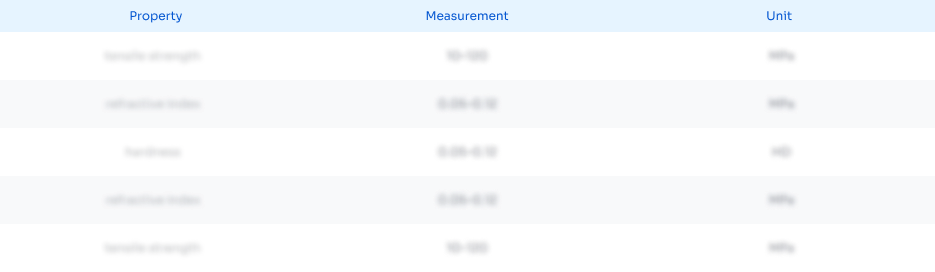
Abstract
Description
Claims
Application Information

- R&D Engineer
- R&D Manager
- IP Professional
- Industry Leading Data Capabilities
- Powerful AI technology
- Patent DNA Extraction
Browse by: Latest US Patents, China's latest patents, Technical Efficacy Thesaurus, Application Domain, Technology Topic, Popular Technical Reports.
© 2024 PatSnap. All rights reserved.Legal|Privacy policy|Modern Slavery Act Transparency Statement|Sitemap|About US| Contact US: help@patsnap.com