Floating double-shaft shoulder friction stir welding tool and method for space welding
A welding tool and friction stir technology, which is applied in the field of floating double-shaft shoulder friction stir welding tools, can solve problems such as difficulties, inability to perform welding, and inability to realize floating welding, etc., and achieve the effect of reducing friction and realizing all-position welding in space
- Summary
- Abstract
- Description
- Claims
- Application Information
AI Technical Summary
Problems solved by technology
Method used
Image
Examples
Embodiment Construction
[0023] Such as Figure 1-Figure 3 As shown, the floating double-shaft shoulder friction stir welding tool for space welding according to the present invention includes a stirring head 1 with an integrally formed connecting shaft 11 and is movably sleeved on the connecting shaft 11 of the stirring head 1 and The sleeve 2 whose inner diameter is the same as the outer diameter of the connecting shaft 11 of the stirring head 1, wherein at least two rolling bearings 3 are arranged at intervals along the axial direction on the connecting shaft 11 of the stirring head 1, in this embodiment, the Five rolling bearings 3 are arranged at equal intervals in the axial direction, and a platform 12 is arranged on the connecting shaft 11 of the stirring head 1 in the axial direction, and the five rolling bearings 3 are located on the platform 12 and along the direction of the platform 12. The length direction is center-symmetrically distributed, and the platform 12 is provided with the same n...
PUM
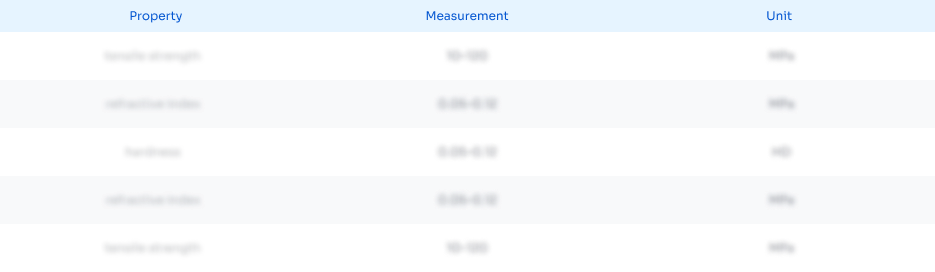
Abstract
Description
Claims
Application Information

- R&D Engineer
- R&D Manager
- IP Professional
- Industry Leading Data Capabilities
- Powerful AI technology
- Patent DNA Extraction
Browse by: Latest US Patents, China's latest patents, Technical Efficacy Thesaurus, Application Domain, Technology Topic, Popular Technical Reports.
© 2024 PatSnap. All rights reserved.Legal|Privacy policy|Modern Slavery Act Transparency Statement|Sitemap|About US| Contact US: help@patsnap.com