A Method for Determining the Machining Position of a Gear Shaft Keyway
A technology for processing position and determining method, applied in metal processing, metal processing equipment, metal processing mechanical parts, etc., can solve the problems of low accuracy of keyway processing position, affecting the service life of gear shaft, and keyway processing position error, etc. To achieve the effect of high measurement accuracy, convenient processing, and ensuring accuracy
- Summary
- Abstract
- Description
- Claims
- Application Information
AI Technical Summary
Problems solved by technology
Method used
Image
Examples
Embodiment Construction
[0033] Below in conjunction with accompanying drawing and embodiment the present invention will be further described:
[0034] like Figure 1-5 As shown, a method for determining the machining position of a gear shaft keyway includes the following steps:
[0035] (1) Manufacture alignment process shaft
[0036] Set the modulus of gear shaft 1 and gear 2 to be processed as m (unit: mm), the tooth width as L1 (unit: mm), and the diameter of the addendum circle as d1 (unit: mm); the diameter of the alignment process shaft is D (unit: mm), the length is L (unit: mm);
[0037] Calibration process shaft diameter range: 1.8*m≤D≤2.5*m (unit: mm);
[0038] Alignment process axis length range: L≥L1+d1 / 2 (unit: mm);
[0039] By replacing the traditional gear model 15 with the design of the process shaft, the structure is simpler and the processing cost is lower;
[0040] (2) Install the gear shaft 1 to be processed
[0041] Place the gear shaft 1 to be processed horizontally on the...
PUM
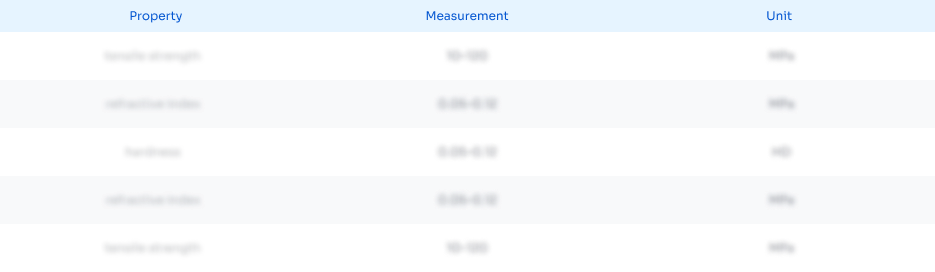
Abstract
Description
Claims
Application Information

- Generate Ideas
- Intellectual Property
- Life Sciences
- Materials
- Tech Scout
- Unparalleled Data Quality
- Higher Quality Content
- 60% Fewer Hallucinations
Browse by: Latest US Patents, China's latest patents, Technical Efficacy Thesaurus, Application Domain, Technology Topic, Popular Technical Reports.
© 2025 PatSnap. All rights reserved.Legal|Privacy policy|Modern Slavery Act Transparency Statement|Sitemap|About US| Contact US: help@patsnap.com