Manufacturing method of brick wall with high shear resistance and shock resistance
A manufacturing method and high seismic technology, applied in the field of masonry walls, can solve problems such as poor shear performance and seismic performance, and achieve the effects of improving seismic performance, improving shear performance, and improving shear performance.
- Summary
- Abstract
- Description
- Claims
- Application Information
AI Technical Summary
Problems solved by technology
Method used
Image
Examples
Embodiment 1
[0041] The present embodiment has the manufacturing method of the masonry wall with high seismic resistance and high shear resistance, and the specific steps are:
[0042] 1) Immerse the brick test block with water;
[0043] 2) Simultaneously prepare masonry mortar, and masonry mortar adopts PVA-ECC:
[0044] ① According to the mass ratio of water: cement: fly ash: quartz sand: water reducing agent: fiber = 1:1.83:2.197:1.463:0.024; 0.063 to weigh the raw materials;
[0045] ②Put the weighed cement, fly ash and quartz sand into the mixing pot and dry for 3 to 5 minutes, until the mixing is uniform, and the speed of the mixing pot is about 40 rpm;
[0046] ③ Then add the weighed water and water reducing agent, stir for 6 minutes until the water reducing agent is fully effective;
[0047] ④ Finally, put in the PVA fibers, adjust the speed of the stirring pot to about 60 rpm, and wet-mix for 5 to 7 minutes until the PVA fibers are evenly dispersed;
[0048] 3) After the prepar...
Embodiment 2
[0061] Example 2 adopts the same test method, test procedure and test specimen as in Example 1, except that the masonry mortar is traditional cement mortar, and the composition mass ratio is water:cement:sea sand=1-3:1:1.375, The plastering mortar is also traditional cement mortar, and the composition mass ratio is water:cement:sea sand=1-3:1:3.
Embodiment 3
[0063] Example 3 adopts the same test method, test procedure and test specimen as in Example 1, except that the plastering mortar is traditional cement mortar, and the composition mass ratio is water:cement:sea sand=1-3:1:3.
PUM
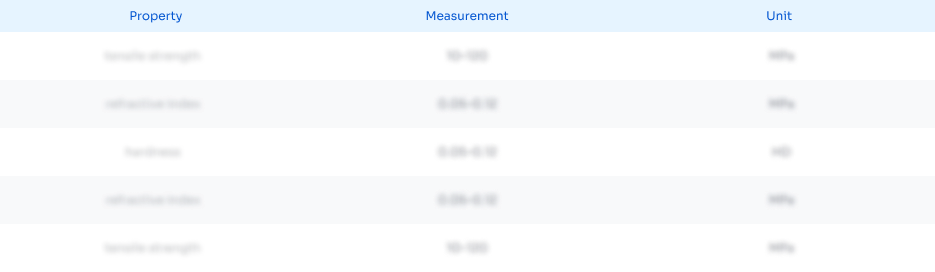
Abstract
Description
Claims
Application Information

- R&D
- Intellectual Property
- Life Sciences
- Materials
- Tech Scout
- Unparalleled Data Quality
- Higher Quality Content
- 60% Fewer Hallucinations
Browse by: Latest US Patents, China's latest patents, Technical Efficacy Thesaurus, Application Domain, Technology Topic, Popular Technical Reports.
© 2025 PatSnap. All rights reserved.Legal|Privacy policy|Modern Slavery Act Transparency Statement|Sitemap|About US| Contact US: help@patsnap.com