A punching and feeding mechanism for automobile beam welding sub-assembly
A technology of feeding mechanism and sub-assembly, which is applied to vehicle parts, feeding devices, manufacturing tools, etc., can solve the problems of easy deviation, irregular and special-shaped structure, and reduce the performance of the whole vehicle, so as to achieve stable adjustment of feeding height and avoid Stamping work, the effect of reducing the risk
- Summary
- Abstract
- Description
- Claims
- Application Information
AI Technical Summary
Problems solved by technology
Method used
Image
Examples
Embodiment Construction
[0014] refer to Figure 1 to Figure 2 , Figure 1 to Figure 2 It is a structural schematic diagram of a specific embodiment of the present invention.
[0015] Such as Figure 1 to Figure 2 As shown, a stamping and feeding mechanism for automobile crossbeam welding subassembly includes a pick-up rotating disk 10, and the two sides of the pick-up rotating disk 10 are respectively a driving connection surface 11 and a pick-up operation surface 12. On the pick-up operation surface 12 of the rotating disk 10, several pick-up operation support arms 20 are arranged, and each of the pick-up operation support arms 20 includes a pick-up support arm towards the axis of the pick-up rotating disk 10 The inner surface 21 and the outer surface 22 of the pick-up support arm facing away from the axis of the pick-up rotating disc 10, each of the pick-up operation support arms 20 is provided with two V The two ends of each described V-shaped connecting rod 30 are respectively the fixed end 31...
PUM
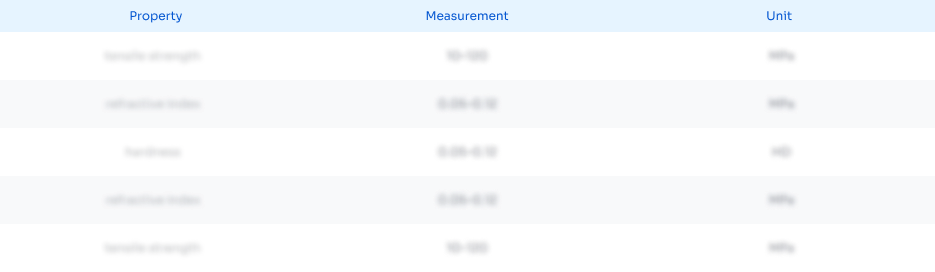
Abstract
Description
Claims
Application Information

- R&D
- Intellectual Property
- Life Sciences
- Materials
- Tech Scout
- Unparalleled Data Quality
- Higher Quality Content
- 60% Fewer Hallucinations
Browse by: Latest US Patents, China's latest patents, Technical Efficacy Thesaurus, Application Domain, Technology Topic, Popular Technical Reports.
© 2025 PatSnap. All rights reserved.Legal|Privacy policy|Modern Slavery Act Transparency Statement|Sitemap|About US| Contact US: help@patsnap.com