Metal ultra-thin strip rolling mill with selectable driving modes and rolling method thereof
A transmission method and metal pole technology, applied in the direction of metal rolling, metal rolling, metal rolling racks, etc., can solve the problems of high technical threshold and risk, large investment, high purchase, operation and maintenance costs
- Summary
- Abstract
- Description
- Claims
- Application Information
AI Technical Summary
Problems solved by technology
Method used
Image
Examples
Embodiment 1
[0054] The structure of the metal ultra-thin strip mill with optional transmission mode is as follows figure 1 , 2 As shown in and 3, the transmission principle of the work roll transmission mode is as follows Figure 4 As shown, the transmission principle of the supporting roller transmission method is as follows Figure 5 As shown, the transmission principle of the compound gearbox is as follows Image 6 with 7 As shown, the sectional structure of the transmission part of the compound gearbox is as Figure 8 As shown, it includes a rolling mill mechanical part 1 and a control system. The rolling mill mechanical part 1 includes a base 5, an arch 7, a first main drive motor 14, a second main drive motor 15, a first main reducer 12, and a second main reducer Machine 13, upper work roll 34, lower work roll 35, upper support roll 33, lower support roll 36, compound gear box 11, pressing device, balance device, roll changing device, first tension motor 23, second tension motor 16 ,...
Embodiment 2
[0077] The device structure is the same as in Example 1;
[0078] The rolling method using the above device is: the rolled piece is 201 stainless steel, the initial thickness is 0.3mm, the width is 300mm, the diameter of the upper and lower work rolls is 120mm, the upper and lower support rolls The diameter is 400mm, the target thickness of the rolled piece is 30μm, and the work roll transmission mode is adopted:
[0079] 1. Use universal joints to connect the upper work roll corresponding output shaft 40 and the lower work roll corresponding output shaft 41 of the composite gear box 11 to the upper work roll 34 and the lower work roll 35 respectively;
[0080] 2. Put the rolled piece in a roll on a drum, and wind one end of the rolled piece through the gap between the upper work roll 34 and the lower work roll 35 on the other side of the drum;
[0081] 3. Start the power supply of the ultra-thin strip rolling mill, set the speed of the upper work roll 34 and the lower work roll 35 to...
PUM
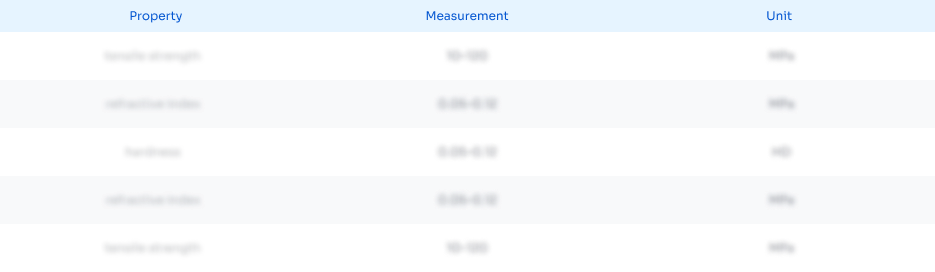
Abstract
Description
Claims
Application Information

- R&D
- Intellectual Property
- Life Sciences
- Materials
- Tech Scout
- Unparalleled Data Quality
- Higher Quality Content
- 60% Fewer Hallucinations
Browse by: Latest US Patents, China's latest patents, Technical Efficacy Thesaurus, Application Domain, Technology Topic, Popular Technical Reports.
© 2025 PatSnap. All rights reserved.Legal|Privacy policy|Modern Slavery Act Transparency Statement|Sitemap|About US| Contact US: help@patsnap.com