Core-shell structure thionazin composite microspheres and preparation method thereof
A core-shell structure and composite technology, which is applied in the field of synthesis of new catalytic materials, can solve the problems of sulfur loss of sulfide catalysts, and achieve the effects of good shape, reduced risk, and improved recycling rate
- Summary
- Abstract
- Description
- Claims
- Application Information
AI Technical Summary
Problems solved by technology
Method used
Image
Examples
Embodiment 1
[0036] ZnS@Ni 2 Preparation of P-complex microspheres:
[0037] Step 1, prepare ZnS microspheres: 0.876g Zn(CH 3COO) 2 2H 2 O was dissolved in 60mL of deionized water. While stirring, 1.8mL of acetic acid and 6mmol of thiourea were added successively, and the stirring was continued until the solution was transparent and colorless. Then, the mixture solution was transferred to a hydrothermal reaction kettle and treated at 170°C for 8h. The resulting white precipitate was centrifuged with absolute ethanol and distilled water, washed several times, and dried in a vacuum oven at 60° C. for 6 hours to obtain white ZnS powder.
[0038] Step 2: Preparation of core-shell structure ZnS@Ni 2 P composite microspheres: Disperse 0.0585 g of the zinc sulfide powder prepared in step 1 into 18 mL of deionized water, and ultrasonically treat it for 20 min. Under magnetic stirring, sequentially add 0.0891g NiCl 2 ·6H 2 O, 0.0788g citric acid and 0.15g sodium dodecyl sulfate (SDS), after ...
Embodiment 2
[0041] ZnS@Ni 2 Preparation of P-complex microspheres:
[0042] In Example 1, the hydrothermal treatment temperature in step 1 was changed to 100°C, and the hydrothermal treatment time was changed to 2h; the hydrothermal treatment temperature in step 2 was changed to 100°C, and the hydrothermal treatment time was changed to 2h, and the obtained product was ZnS@Ni with inhomogeneous morphology. 2 P Composite Microspheres.
Embodiment 3
[0044] ZnS@Ni 2 Preparation of P-complex microspheres:
[0045] In Example 1, the hydrothermal treatment temperature in step 1 was changed to 220°C, and the hydrothermal treatment time was changed to 16h; the hydrothermal treatment temperature in step 2 was changed to 220°C, and the hydrothermal treatment time was changed to 20h, and the obtained product was ZnS@Ni with uniform morphology 2 P composite microspheres.
PUM
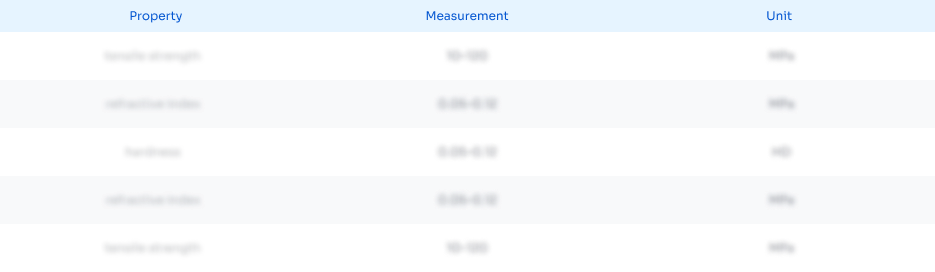
Abstract
Description
Claims
Application Information

- R&D
- Intellectual Property
- Life Sciences
- Materials
- Tech Scout
- Unparalleled Data Quality
- Higher Quality Content
- 60% Fewer Hallucinations
Browse by: Latest US Patents, China's latest patents, Technical Efficacy Thesaurus, Application Domain, Technology Topic, Popular Technical Reports.
© 2025 PatSnap. All rights reserved.Legal|Privacy policy|Modern Slavery Act Transparency Statement|Sitemap|About US| Contact US: help@patsnap.com