A method for single-shot smelting tc4 titanium alloy ingots in an electron beam cold hearth furnace
An electron beam cooling hearth furnace and titanium alloy technology is applied in the field of TC4 titanium alloy ingot casting and electron beam cooling hearth furnace single-melting TC4 titanium alloy ingot casting field, which can solve the problems of raw material quality decline, unevenness, pollution, etc., and achieve The effect of reducing production costs
- Summary
- Abstract
- Description
- Claims
- Application Information
AI Technical Summary
Problems solved by technology
Method used
Image
Examples
Embodiment 1
[0056] A method for single-shot smelting of TC4 titanium alloy ingots in an electron beam cold hearth furnace, comprising the steps of:
[0057] Step 1: Raw material preparation
[0058] Weigh 960kg of raw materials according to the following weight percentages, 88.0% to 90.0% of titanium sponge, 5.5% to 7.0% of V-Al master alloy, and 3.0% to 7.0% of aluminum beans;
[0059] Step 2: Compress raw materials into blocks
[0060] After mixing the titanium sponge, V-Al master alloy, and aluminum beans described in step 1, press them into blocks on a hydraulic press;
[0061] Step 3: Put the block into the bin and dry
[0062] Put the blocks pressed in step 2 into 4 blocks per row, put them in a single layer and put them into the material box, then dry the blocks for 2 to 4 hours at a temperature of 115 to 125°C;
[0063] Step 4: Electron Beam Cold Hearth Furnace Melting
[0064] Send the dried block in step 3 into an electron beam cold hearth furnace for smelting, and obtain TC...
PUM
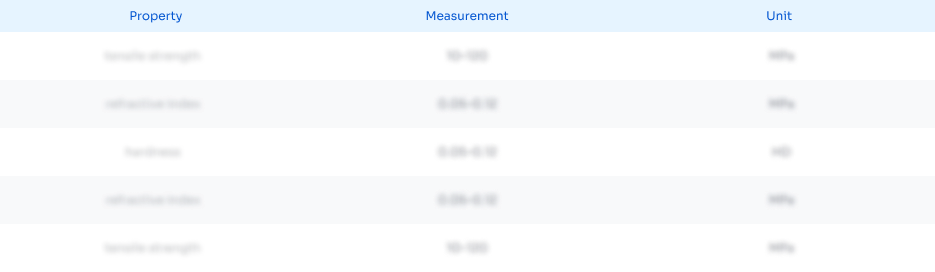
Abstract
Description
Claims
Application Information

- Generate Ideas
- Intellectual Property
- Life Sciences
- Materials
- Tech Scout
- Unparalleled Data Quality
- Higher Quality Content
- 60% Fewer Hallucinations
Browse by: Latest US Patents, China's latest patents, Technical Efficacy Thesaurus, Application Domain, Technology Topic, Popular Technical Reports.
© 2025 PatSnap. All rights reserved.Legal|Privacy policy|Modern Slavery Act Transparency Statement|Sitemap|About US| Contact US: help@patsnap.com