Organosilicon-based solvent for removing carbon dioxide from flue gas, and process thereof
A technology based on carbon dioxide and organosilicon, applied in air quality improvement, chemical instruments and methods, and separation of dispersed particles, can solve problems such as increased regeneration energy consumption, increased solvent viscosity, and increased total reaction heat, and achieve low raw material Effects of cost, low regeneration energy consumption, and high CO2 absorption capacity
- Summary
- Abstract
- Description
- Claims
- Application Information
AI Technical Summary
Problems solved by technology
Method used
Image
Examples
Embodiment 1
[0032] Dissolve divinyltetramethylsiloxane (50 g) in 200 mL CHCl 3 , into a three-necked flask equipped with a magnetic stir bar. The reaction flask was placed in ice water, kept at 0 °C, m-chloroperoxybenzoic acid (150 g) was dissolved in 1 L CHCl 3 After filtration, the filtrate was slowly added dropwise to the reaction flask for 1.5 h, and the reaction solution was stirred overnight. 2 L of 5% Na for the reaction solution 2 CO 3 Extract the organic layer with anhydrous MgSO 4 After drying, it was filtered and concentrated under reduced pressure. Add hexane, filter off the residual m-chloroperoxybenzoic acid, and cool the filtrate at low temperature to obtain tetramethylsiloxane whose end group is a dioxirane group.
[0033] Dissolve oxirane-terminated tetramethylsiloxane (10 g) in 100 mL of anhydrous tetrahydrofuran, add dropwise ethylenediamine (20 g) in 100 mL of anhydrous tetrahydrofuran solution, dropwise for 1 h, and react the solution in Reflux at 70 °C for one ...
Embodiment 2
[0036] Vinyltetramethylsiloxane (25 g) was dissolved in 50 mL CHCl 3 , into a three-necked flask equipped with a magnetic stir bar. The reaction bottle was placed in ice water, kept warm at 0 °C, m-chloroperoxybenzoic acid (10% excess) was dissolved in 500 mL CHCl 3 After filtration, the filtrate was slowly added dropwise to the reaction flask for 1 h, and the reaction solution was stirred overnight. 2 L of 5% Na for the reaction solution 2 CO 3 Extraction, the organic layer with anhydrous MgSO 4 After drying, it was filtered and concentrated under reduced pressure. Add hexane, filter off the residual m-chloroperoxybenzoic acid, and cool the filtrate at low temperature to obtain tetramethylsiloxane whose end group is an oxirane group.
[0037] Ethylenediamine (15 g) was dissolved in 100 mL of isopropanol and 5 mL of water, and 100 mL of isopropanol solution of tetramethylsiloxane terminated in epoxy group was added dropwise, and the reaction solution was refluxed at 70 °C...
Embodiment 3
[0040] Absorption of CO by bubbling 2Experiment, solvent weight gain ratio is shown in Table 1.
[0041] Table 1 Solvent absorption of CO 2 Weight gain ratio
[0042]
[0043] -- Dry: CO 2 Pass through dryer before reacting with amine
[0044] -- wet: CO 2 Pass through a water saturator before reacting with amine
PUM
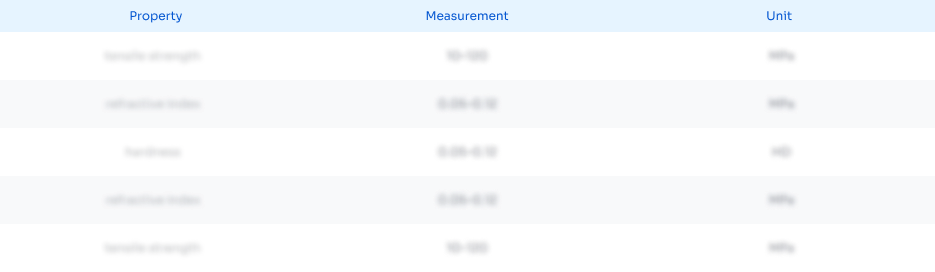
Abstract
Description
Claims
Application Information

- R&D
- Intellectual Property
- Life Sciences
- Materials
- Tech Scout
- Unparalleled Data Quality
- Higher Quality Content
- 60% Fewer Hallucinations
Browse by: Latest US Patents, China's latest patents, Technical Efficacy Thesaurus, Application Domain, Technology Topic, Popular Technical Reports.
© 2025 PatSnap. All rights reserved.Legal|Privacy policy|Modern Slavery Act Transparency Statement|Sitemap|About US| Contact US: help@patsnap.com