Preparation method of amination graphene oxide reinforced fibers
A technology for reinforcing fibers and oxide stones, applied in the field of fiber reinforcement, can solve the problems of decreased fiber strength, easy agglomeration, insufficient bonding force between nano-fillers and matrix, and achieve the effect of performance enhancement.
- Summary
- Abstract
- Description
- Claims
- Application Information
AI Technical Summary
Problems solved by technology
Method used
Examples
Embodiment 1
[0020] A preparation method of graphene reinforced fiber, comprising:
[0021] (1) Mix the flake graphite of 2 weight parts, the concentrated sulfuric acid of 300 weight parts and the phosphoric acid of 30 weight parts, slowly add the potassium permanganate of 15 weight parts, stir at 45 ℃ for 9 hours;
[0022] (2) At 0° C., add 300 parts by weight of deionized water and 20 parts by weight of hydrogen peroxide at a concentration of 10 wt % to the mixture, and stir for 5 minutes;
[0023] (3) separate and successively wash the product with deionized water, hydrochloric acid of 10wt% concentration and absolute ethanol, and vacuum-dry to obtain graphene oxide;
[0024] (4) Disperse the graphene oxide in 15 parts by weight of N,N-dimethylformamide solution, add 40 parts by weight of SOCl at 0°C 2 , after mixing evenly, the temperature was raised to 65°C, and the stirring was continued for 30 hours;
[0025] (5) Add 1,6 hexamethylenediamine dropwise to the above mixture, stir at ...
Embodiment 2
[0031] A preparation method of graphene reinforced fiber, comprising:
[0032] (1) 5 parts by weight of flake graphite, the concentrated sulfuric acid of 500 parts by weight and the phosphoric acid of 60 parts by weight are mixed uniformly, slowly add the potassium permanganate of 20 parts by weight, and stir at 55 DEG C for 18 hours;
[0033] (2) At 5°C, add 500 parts by weight of deionized water and 50 parts by weight of hydrogen peroxide at a concentration of 30 wt% to the mixture, and stir for 10 minutes;
[0034] (3) separate and wash the product successively with deionized water, 30wt% concentration of hydrochloric acid and absolute ethanol, and vacuum-dry to obtain graphene oxide;
[0035] (4) Disperse the graphene oxide in 20 parts by weight of N,N-dimethylformamide solution, add 60 parts by weight of SOCl at 5°C 2 , after mixing evenly, the temperature was raised to 80°C, and the stirring was continued for 40 hours;
[0036] (5) Add 1,6 hexamethylenediamine dropwise...
Embodiment 3
[0042] A preparation method of graphene reinforced fiber, comprising:
[0043] (1) The flake graphite of 3 weight parts, the concentrated sulfuric acid of 400 weight parts and the phosphoric acid of 50 weight parts are mixed uniformly, slowly add the potassium permanganate of 17 weight parts, stir 12 hours at 50 ℃;
[0044] (2) At 0° C., add 400 parts by weight of deionized water and 30 parts by weight of hydrogen peroxide at a concentration of 20 wt % to the mixture, and stir for 7 minutes;
[0045] (3) separate and wash the product successively with deionized water, hydrochloric acid of 20wt% concentration and absolute ethanol, and vacuum-dry to obtain graphene oxide;
[0046] (4) Disperse the graphene oxide in 16 parts by weight of N,N-dimethylformamide solution, add 50 parts by weight of SOCl at 0°C 2 , after mixing evenly, the temperature was raised to 70°C, and the stirring was continued for 35 hours;
[0047] (5) Add 1,6-hexamethylenediamine dropwise to the above mixt...
PUM
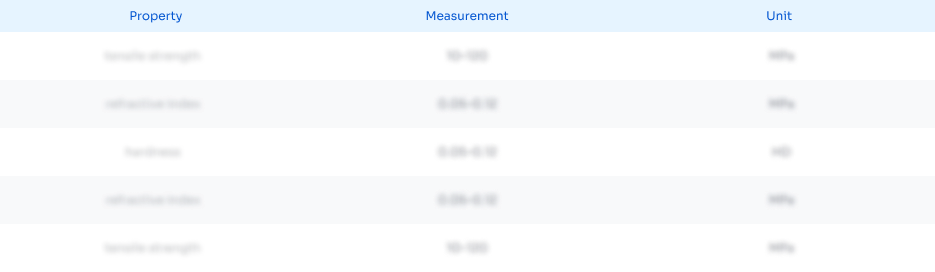
Abstract
Description
Claims
Application Information

- Generate Ideas
- Intellectual Property
- Life Sciences
- Materials
- Tech Scout
- Unparalleled Data Quality
- Higher Quality Content
- 60% Fewer Hallucinations
Browse by: Latest US Patents, China's latest patents, Technical Efficacy Thesaurus, Application Domain, Technology Topic, Popular Technical Reports.
© 2025 PatSnap. All rights reserved.Legal|Privacy policy|Modern Slavery Act Transparency Statement|Sitemap|About US| Contact US: help@patsnap.com