A wind turbine load shedding control method
A wind turbine and control method technology, applied in wind turbine control, engine control, wind power generation, etc., can solve the problems of increased fatigue load, delayed control effect, overspeed, etc., to reduce mechanical fatigue, reduce operating load, and solve the problem of execution lag effect
- Summary
- Abstract
- Description
- Claims
- Application Information
AI Technical Summary
Problems solved by technology
Method used
Image
Examples
Embodiment Construction
[0017] The present invention will be further described below in conjunction with accompanying drawing.
[0018] With reference to accompanying drawing: a kind of wind turbine load shedding control method, it comprises the following steps:
[0019] Step 1. The wind turbine enters the double closed-loop control mode;
[0020] Step 2. Determine whether the generating power of the wind turbine is above k.Pu, if so, go to step 3, otherwise return to step 1; k is the set control coefficient, the range is 0
[0021] Step 3. Determine whether the current feedback value of the pitch motor is greater than the set reference value Ir, if so, enter step 4, otherwise return to step 1;
[0022] Step 4. The wind turbine enters the semi-control mode operation, that is, when the actual feedback current of the pitch motor is greater than the reference value Ir, the pitch motor is controlled to output according to the reference value Ir,...
PUM
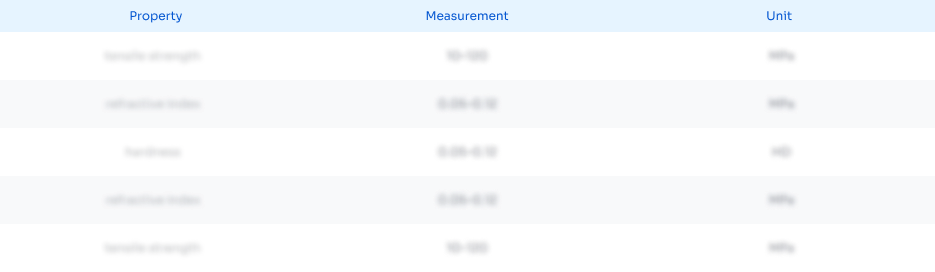
Abstract
Description
Claims
Application Information

- R&D
- Intellectual Property
- Life Sciences
- Materials
- Tech Scout
- Unparalleled Data Quality
- Higher Quality Content
- 60% Fewer Hallucinations
Browse by: Latest US Patents, China's latest patents, Technical Efficacy Thesaurus, Application Domain, Technology Topic, Popular Technical Reports.
© 2025 PatSnap. All rights reserved.Legal|Privacy policy|Modern Slavery Act Transparency Statement|Sitemap|About US| Contact US: help@patsnap.com