A reflective film material for photovoltaic modules
A thin-film material and photovoltaic module technology, applied in the field of solar energy, can solve the problems of cost reduction of reflective tape, complex process, and low product quality rate, and achieve the effects of reducing conversion efficiency loss, increasing light intensity and area, and low manufacturing cost
- Summary
- Abstract
- Description
- Claims
- Application Information
AI Technical Summary
Problems solved by technology
Method used
Image
Examples
Embodiment 1
[0037] A reflective thin film material used for photovoltaic modules, the preparation steps of which are as follows:
[0038] Step 1, adding polyethylene terephthalate and polysilazane to a low molecular weight solvent, stirring for 2 hours;
[0039] Step 2, adding a coupling agent, an initiator and a catalyst to the solution obtained in step 1, sealing the protective gas and reacting under pressure for 2 hours to obtain a reaction solution;
[0040] Step 3, adding metal fillers, organic titanium salts and dispersants into the reaction solution and stirring evenly, then performing high-temperature methane reflux aeration reaction for 3 hours;
[0041] Step 4, after natural cooling, aging the reaction solution at low temperature for 5 hours;
[0042] Step 5, adding carbene to the reaction solution, stirring at low temperature, aeration and dispersion reaction;
[0043] Step 6, the reaction solution after the reaction in step 5 is pulled and coated on the substrate, and then d...
Embodiment 2
[0061] A reflective thin film material used for photovoltaic modules, the preparation steps of which are as follows:
[0062] Step 1, adding polyethylene terephthalate and polysilazane to a low molecular weight solvent, and stirring for 4 hours;
[0063] Step 2, adding a coupling agent, an initiator and a catalyst to the solution obtained in step 1, sealing the protective gas and reacting under pressure for 5 hours to obtain a reaction solution;
[0064] Step 3, adding the metal filler, organic titanium salt and dispersant into the reaction solution and stirring evenly, then performing high-temperature methane reflux aeration reaction for 6 hours;
[0065] Step 4, after natural cooling, aging the reaction solution at low temperature for 8 hours;
[0066] Step 5, adding carbene to the reaction solution, stirring at low temperature, aeration and dispersion reaction;
[0067] Step 6, pulling the coating film on the substrate with the reaction solution after the reaction in step...
Embodiment 3
[0085] A reflective thin film material used for photovoltaic modules, the preparation steps of which are as follows:
[0086] Step 1, adding polyethylene terephthalate and polysilazane to a low molecular weight solvent, and stirring for 3 hours;
[0087] Step 2, adding a coupling agent, an initiator and a catalyst to the solution obtained in step 1, sealing the protective gas and reacting under pressure for 4 hours to obtain a reaction solution;
[0088] Step 3, adding metal filler, organic titanium salt and dispersant to the reaction solution and stirring evenly, then performing high-temperature methane reflux aeration reaction for 4 hours;
[0089] Step 4, after natural cooling, aging the reaction solution at low temperature for 6 hours;
[0090] Step 5, adding carbene to the reaction solution, stirring at low temperature, aeration and dispersion reaction;
[0091] In step 6, the reaction solution after the reaction in step 5 is pulled and coated on the substrate, and then...
PUM
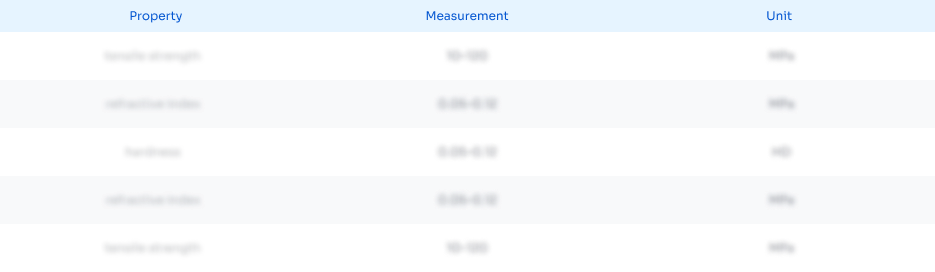
Abstract
Description
Claims
Application Information

- R&D Engineer
- R&D Manager
- IP Professional
- Industry Leading Data Capabilities
- Powerful AI technology
- Patent DNA Extraction
Browse by: Latest US Patents, China's latest patents, Technical Efficacy Thesaurus, Application Domain, Technology Topic, Popular Technical Reports.
© 2024 PatSnap. All rights reserved.Legal|Privacy policy|Modern Slavery Act Transparency Statement|Sitemap|About US| Contact US: help@patsnap.com