Method for zeroing initial null voltage of bridge sensor
A bridge sensor, initial zero technology, applied in the field of sensors, can solve the problems of inability to achieve accurate measurement, saturation of operational amplifiers, weak voltage signals, etc., to achieve the effect of improving high overload resistance, high reception, and increasing service life
- Summary
- Abstract
- Description
- Claims
- Application Information
AI Technical Summary
Problems solved by technology
Method used
Image
Examples
Embodiment 1
[0033] The present invention provides a method that can stably, reliably and quickly complete the zeroing of the bridge sensor. The specific implementation is as follows:
[0034] The resistances of the four arms of the Wheatstone bridge are , , , , using DC power supply, the power supply voltage is , the zero output voltage is , when the sensor input signal is zero, there is
[0035]
[0036] when , that is, there is a zero voltage, and the sensor needs to be zeroed.
[0037] According to the actual situation, the present invention adopts the manual hardware zeroing method to complete the zeroing work in the production process of the sensor. During the zeroing process, the average resistance value of the arm resistance of the Wheatstone bridge needs to be measured, and the zeroing resistance is calculated by the formula The size of the zero-adjustment resistance should be determined reasonably, so that the zero-adjustment resistance R can be combined with as ...
example 1
[0064] Example 1: In the sensor production process, the measured input resistance , output resistance , the initial zero voltage , The sensor is powered by a 3.3V DC power supply.
[0065] by the formula
[0066]
[0067]
[0068] Select 32 from the zeroing resistor sequence 、18 , 1.8 The resistors are connected in series to form a zeroing resistor R=51.8 .
example 2
[0069] Example 2: In the sensor production process, the measured input resistance , output resistance , the initial zero voltage , The sensor is powered by a 3.3V DC power supply.
[0070] by the formula
[0071]
[0072]
[0073] Pick 100 from the zeroing resistor sequence The resistance directly gets the zeroing resistance R=100 .
[0074] Connect the combined resistor R in parallel to a bridge with a higher potential (such as Figure II ), the measured initial output voltage of the bridge sensor after zeroing is less than 1 . After fixing the parallel resistance R, it can be packaged, and the zero adjustment work is completed, and then the subsequent work such as sensor calibration is performed.
PUM
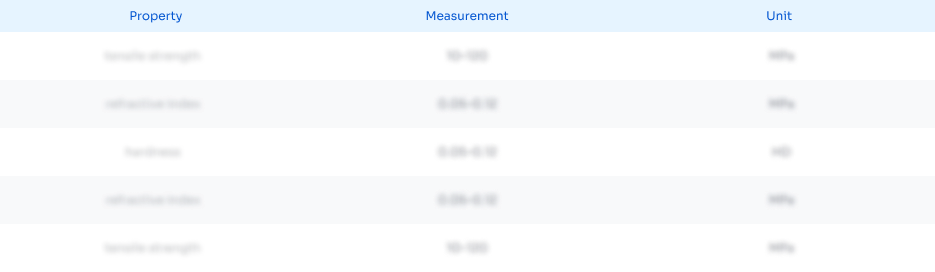
Abstract
Description
Claims
Application Information

- Generate Ideas
- Intellectual Property
- Life Sciences
- Materials
- Tech Scout
- Unparalleled Data Quality
- Higher Quality Content
- 60% Fewer Hallucinations
Browse by: Latest US Patents, China's latest patents, Technical Efficacy Thesaurus, Application Domain, Technology Topic, Popular Technical Reports.
© 2025 PatSnap. All rights reserved.Legal|Privacy policy|Modern Slavery Act Transparency Statement|Sitemap|About US| Contact US: help@patsnap.com