A pressure-stabilizing pilot relief valve
A technology of pilot-operated relief valve and pilot-operated valve, which is applied in the direction of fluid pressure actuators, servo motor components, mechanical equipment, etc., can solve the problems of large pressure adjustment deviation, influence on pressure stability, and low flow rate, etc., to achieve Reduce the probability of howling and increase the effect of stability
- Summary
- Abstract
- Description
- Claims
- Application Information
AI Technical Summary
Problems solved by technology
Method used
Image
Examples
Embodiment Construction
[0023] The present invention will be further described in detail below in conjunction with the accompanying drawings and embodiments.
[0024] In order to solve the problems of unstable pressure and whistling in the prior art pilot-operated relief valve, the present invention provides a stable-pressure pilot-operated relief valve, such as figure 1 As shown, including main valve 10, pilot valve 30, comparator 20, system hydraulic pressure source 50 respectively acts on the spool of main valve 10, pilot valve 30, comparator 20, comparator 20 is connected with pilot valve 30, comparator 20 Dynamic adjustments are made according to changes in the inlet pressure or flow of the relief valve, so that the inlet pressure acting on the main valve 10 is considered stable within the allowable error. Wherein, a feedback spring is provided between the comparator 20 and the pilot valve 30 to keep the pressure at the upper and lower sides of the main valve core 14 of the main valve 10 constan...
PUM
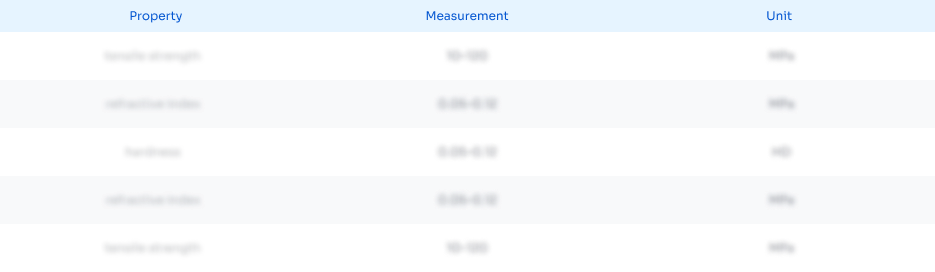
Abstract
Description
Claims
Application Information

- R&D
- Intellectual Property
- Life Sciences
- Materials
- Tech Scout
- Unparalleled Data Quality
- Higher Quality Content
- 60% Fewer Hallucinations
Browse by: Latest US Patents, China's latest patents, Technical Efficacy Thesaurus, Application Domain, Technology Topic, Popular Technical Reports.
© 2025 PatSnap. All rights reserved.Legal|Privacy policy|Modern Slavery Act Transparency Statement|Sitemap|About US| Contact US: help@patsnap.com