PTFE (polytetrafluoroethylene) foaming coating finishing agent and preparation method of composite filter of coating thereof
A technology of foam coating and PTFE, which is applied in the field of preparation of PTFE foam coating finishing agent and its coated composite filter material, can solve the problem of inability to prolong the life of the filter material, complex preparation procedures, and inability to effectively isolate oxygen and moisture and other problems, to achieve the effects of prolonging the service life, simple preparation method, and low raw material cost
- Summary
- Abstract
- Description
- Claims
- Application Information
AI Technical Summary
Problems solved by technology
Method used
Image
Examples
Embodiment 1
[0026] Add 800g of distilled water, 20g of NaOH, and 4g of penetrant into the beaker in sequence, and after fully stirring, put the filter material sample into the mixed solution, and place it in a constant temperature water bath at 55°C for 2 hours; The filter material is washed to neutral and dried in an oven at 100°C;
[0027] Add 2g of azodicarbonamide, 0.2g of zinc oxide, 150g of PTFE emulsion, 40g of acrylic resin, and 10g of water-based epoxy resin in proportion to another beaker, and stir evenly. Put the foaming coating solution in an oven at 160°C to foam at a foaming ratio of 1:4 to obtain a foaming coating finish;
[0028] The above-mentioned foam coating finishing agent is evenly coated on the upper surface of the filter material to obtain a foam-coated PTFE composite filter material;
[0029] The foam coating finishing agent is evenly coated on the surface of the filter material, forming a uniform and porous foam layer on the surface of the filter material, which...
Embodiment 2
[0032] Add 800g of distilled water, 40g of NaOH, and 12g of penetrant into the beaker in turn. After fully stirring, put the filter material sample into the mixed solution, and place it in a constant temperature water bath at 50°C for 3 hours; The filter material is washed to neutral, and dried in an oven at 110°C;
[0033] Add 6g of azodicarbonamide, 0.4g of zinc oxide, 130g of PTFE emulsion, 36g of acrylic resin, and 24g of water-based epoxy resin in proportion to another beaker, and stir evenly. Put the foaming coating solution in an oven at 140°C to foam at a foaming ratio of 1:3 to obtain a foaming coating finish;
[0034] The above-mentioned foam coating finishing agent is evenly coated on the upper surface of the filter material to obtain a foam-coated PTFE composite filter material;
[0035] The foam coating finishing agent is evenly coated on the surface of the filter material, forming a uniform and porous foam layer on the surface of the filter material, which impro...
Embodiment 3
[0038] Add 800g of distilled water, 30g of NaOH, and 6g of penetrant into the beaker in turn, and after fully stirring, put the filter material sample into the mixed solution, and place it in a constant temperature water bath at 70°C for 4 hours; The filter material is washed to neutral and dried in an oven at 120°C;
[0039] Add 4g of azodicarbonamide, 0.2g of zinc oxide, 140g of PTFE emulsion, 35g of acrylic resin, and 15g of water-based epoxy resin in proportion to another beaker, and stir evenly. Put the foaming coating solution in an oven at 180°C to foam at a foaming ratio of 1:6 to obtain a foaming coating finish;
[0040] The above-mentioned foam coating finishing agent is evenly coated on the upper surface of the filter material to obtain a foam-coated PTFE composite filter material;
[0041] The foam coating finishing agent is evenly coated on the surface of the filter material, forming a uniform and porous foam layer on the surface of the filter material, which imp...
PUM
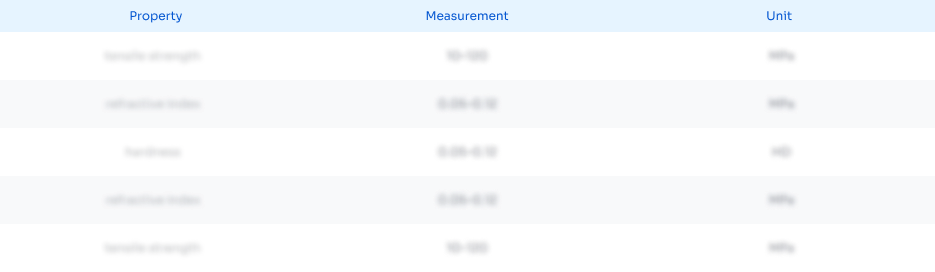
Abstract
Description
Claims
Application Information

- R&D Engineer
- R&D Manager
- IP Professional
- Industry Leading Data Capabilities
- Powerful AI technology
- Patent DNA Extraction
Browse by: Latest US Patents, China's latest patents, Technical Efficacy Thesaurus, Application Domain, Technology Topic, Popular Technical Reports.
© 2024 PatSnap. All rights reserved.Legal|Privacy policy|Modern Slavery Act Transparency Statement|Sitemap|About US| Contact US: help@patsnap.com