Gyro permanent magnet synchronous motor sensorless control system
A permanent magnet synchronous motor and control system technology, applied in the control system, electronic commutation motor control, current controller, etc., can solve the problems of complex methods and low motor speed stability, and achieve improved speed stability and work efficiency Maximize and reduce the effect of torque ripple
- Summary
- Abstract
- Description
- Claims
- Application Information
AI Technical Summary
Problems solved by technology
Method used
Image
Examples
Embodiment Construction
[0025] The present invention aims at the deficiencies of the prior art and proposes a gyro permanent magnet synchronous motor sensorless control system. Compared with the prior art, the gyro motor of the present invention uses a permanent magnet synchronous motor, and the difference between the permanent magnet synchronous motor and the brushless DC motor The difference is that the no-load back EMF waveform of the permanent magnet synchronous motor is a sine wave. According to the working principle of the motor, the best driving method of the permanent magnet synchronous motor is a sine wave drive. Most of the implementation methods of permanent magnet synchronous motor sine wave drive in industrial applications use digital methods such as space vector pulse width modulation or sinusoidal pulse width modulation. Torque fluctuations are caused, which affect the stability of the rotational speed, so it is difficult to meet the extremely high requirements for rotational speed stab...
PUM
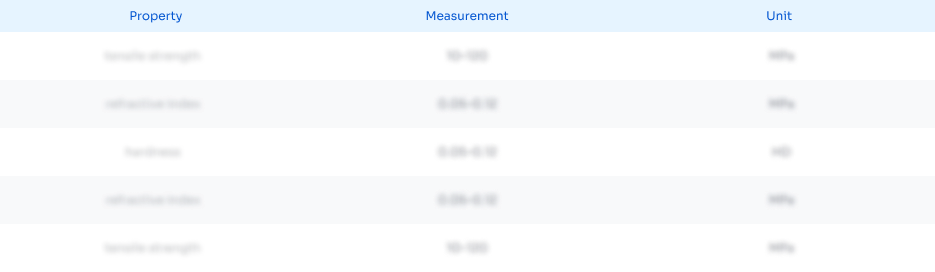
Abstract
Description
Claims
Application Information

- R&D
- Intellectual Property
- Life Sciences
- Materials
- Tech Scout
- Unparalleled Data Quality
- Higher Quality Content
- 60% Fewer Hallucinations
Browse by: Latest US Patents, China's latest patents, Technical Efficacy Thesaurus, Application Domain, Technology Topic, Popular Technical Reports.
© 2025 PatSnap. All rights reserved.Legal|Privacy policy|Modern Slavery Act Transparency Statement|Sitemap|About US| Contact US: help@patsnap.com