Electron frequency drift simulator for laser velocity measurement sensor
A laser speed measurement and sensor technology, applied in the testing/calibration of speed/acceleration/shock measurement equipment, instruments, measuring devices, etc., can solve the problem of difficult to find moving targets and test equipment, high precision requirements for landing navigation measurement, and speed measurement simulation Problems such as difficulty in device design, etc., to achieve the effect of small error, simple structure and high precision
- Summary
- Abstract
- Description
- Claims
- Application Information
AI Technical Summary
Problems solved by technology
Method used
Image
Examples
Embodiment Construction
[0025] The specific embodiment of the present invention is described in further detail below in conjunction with accompanying drawing:
[0026] The present invention is composed of three analog channels, which respectively correspond to the three velocity vector channels of the laser speed measuring sensor. The hardware of the three channels is consistent, and the following only describes one channel:
[0027] The transmitting and receiving module is composed of a transmitting and receiving coupler 1 and a single-mode polarization-maintaining optical fiber 2 . The transmitting and receiving coupler 1 adopts F810FC-1550 from Thorlabs in the United States, with a focal length of 37.13 mm, a numerical aperture of 0.24, an entrance pupil of 8.91 mm, and a converging spot diameter of 10.3 μm. The single-mode polarization-maintaining fiber 2 adopts Corning PM Fibers PI936 of the optical library, the core diameter is 9 μm, and the accepted power is greater than 3W.
[0028] The elec...
PUM
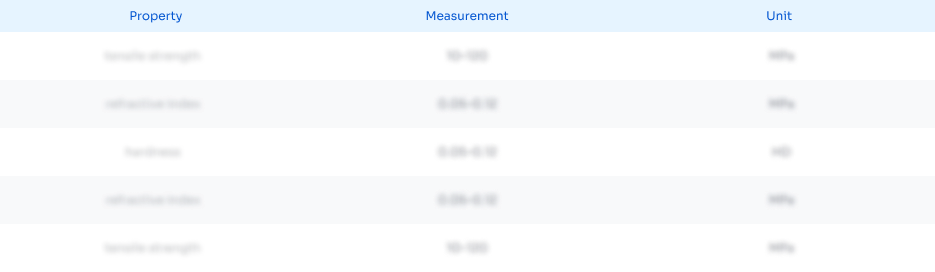
Abstract
Description
Claims
Application Information

- Generate Ideas
- Intellectual Property
- Life Sciences
- Materials
- Tech Scout
- Unparalleled Data Quality
- Higher Quality Content
- 60% Fewer Hallucinations
Browse by: Latest US Patents, China's latest patents, Technical Efficacy Thesaurus, Application Domain, Technology Topic, Popular Technical Reports.
© 2025 PatSnap. All rights reserved.Legal|Privacy policy|Modern Slavery Act Transparency Statement|Sitemap|About US| Contact US: help@patsnap.com