Method for dewatering solvent during aromatic acid production process
A production process, a technology for aromatic acids, which is applied in the separation/purification of carboxylic acid compounds, the preparation of carboxylic acids by oxidation, organic chemistry, etc. It can solve the problems of affecting product quality, high energy consumption of azeotropic distillation process, and reduce steam consumption. , the effect of increasing production capacity and reducing load
- Summary
- Abstract
- Description
- Claims
- Application Information
AI Technical Summary
Problems solved by technology
Method used
Image
Examples
Embodiment 1
[0028] Taking the production process of terephthalic acid (PTA) as an example, PTA uses p-xylene (PX) as a raw material, and is catalytically oxidized under a catalyst and a certain temperature and pressure to prepare each strand of acetic acid aqueous solution from the reaction system and enter the solvent dehydration system.
[0029] Such as figure 1 Shown, the low concentration acetic acid aqueous solution 1 flow rate 5610kg / hr (containing acetic acid 26.92wt.%, water 72.90wt.%, PX 0.09wt.%, methyl acetate 0.09wt.%) from the oxidation reaction system enters the top of extraction tower T1 15895kg / hr (containing acetic acid 0.01wt.%, water 0.05wt.%, PX 95.40wt%, methyl acetate 4.54wt.%) solvent from the bottom of the extraction tower T1 in the T3 tower still of the entrainer refining tower Enter, countercurrent contact in the extraction tower T1, the extraction phase 3 obtained at the top of the extraction tower T1 is 18668kg / hr (containing acetic acid 8.09wt.%, water 6.96wt....
Embodiment 2
[0032] The low-concentration acetic acid aqueous solution 1 flow rate 1700kg / hr (containing acetic acid 20wt.%, water 80wt.%) from the oxidation reaction system enters the top of the extraction tower, and comes from the 3564kg / hr (containing acetic acid 0.01wt. %, water 0.05wt.%, PX95.40wt%, the solvent of methyl acetate 4.54wt.%) enters from the bottom of the extraction tower, countercurrent contacts in the extraction tower, and the extraction tower top obtains the extraction phase 4438kg / hr (containing acetic acid 1.83wt.%, water 2.97wt.%, PX 81.16wt.%, methyl acetate 3.69wt.%), and the bottom of the extraction tower obtains a raffinate phase of 816kg / hr.
[0033] The extraction phase from the top of the extraction tower is 4438kg / hr (containing acetic acid 1.83wt.%, water 2.97wt.%, PX 81.16wt.%, methyl acetate 3.69wt.%) and 34450kg of high-concentration acetic acid aqueous solution from the oxidation reaction system / hr (containing 70.10wt.% of acetic acid, containing 29.46...
Embodiment 3
[0035] In the process of producing terephthalic acid with p-diethylbenzene (PDEB) as raw material, the flow of low-concentration acetic acid aqueous solution 1 from the oxidation reaction system is 3910kg / h (containing 29.92wt.% of acetic acid and 69.82wt.% of water), and enters the extraction At the top of the tower T1, the flow rate of the extraction agent 14 returning to the extraction tower from the tank of the entrainer refining tower T3 is 12264kg / h (containing PDEB 96.01wt.%), and enters the bottom of the extraction tower T1, and is contacted countercurrently in the extraction tower T1. The flow rate of the extract phase 3 obtained from the top of the extraction tower T1 is 14250 kg / h (containing 6.29 wt.% acetic acid, PDEB, 81.19 wt.%), and the flow rate of the raffinate phase 4 obtained from the top of the tower is 1924 kg / h.
[0036] The extraction phase 3 from the top of the extraction tower T1 and the high-concentration acetic acid aqueous solution 5 flow from the o...
PUM
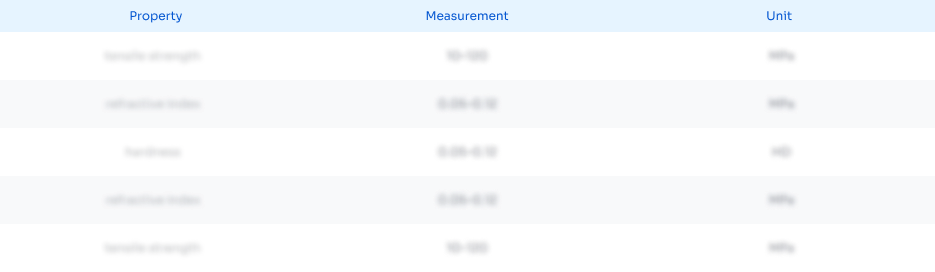
Abstract
Description
Claims
Application Information

- R&D
- Intellectual Property
- Life Sciences
- Materials
- Tech Scout
- Unparalleled Data Quality
- Higher Quality Content
- 60% Fewer Hallucinations
Browse by: Latest US Patents, China's latest patents, Technical Efficacy Thesaurus, Application Domain, Technology Topic, Popular Technical Reports.
© 2025 PatSnap. All rights reserved.Legal|Privacy policy|Modern Slavery Act Transparency Statement|Sitemap|About US| Contact US: help@patsnap.com