Manufacturing method and injection mold for multi-layer lens
A technology of injection mold and manufacturing method, which is applied in the field of optical lenses, and can solve problems such as long cooling and forming time, lens light transmittance, refractive index, difference in clarity, lower lens quality and production efficiency, etc.
- Summary
- Abstract
- Description
- Claims
- Application Information
AI Technical Summary
Problems solved by technology
Method used
Image
Examples
Embodiment Construction
[0023] The specific embodiments of the present invention will be further described below in conjunction with the accompanying drawings. It should be noted here that the descriptions of these embodiments are used to help understand the present invention, but are not intended to limit the invention. In addition, the technical features involved in the various embodiments of the present invention described below may be combined with each other as long as they do not constitute a conflict with each other.
[0024] like figure 1 Shown, a kind of multi-layer lens, comprises basic layer lens 1 and the top layer lens 2 that is positioned at the top layer lens 1, the bottom layer lens 3 that is positioned at the bottom layer lens 1; Laminating and bonding; the edge of the base layer lens 1 is provided with a feed port 11;
[0025] The upper surface and the lower bottom surface of the base lens 1 are respectively provided with injection channels 12, the injection channels 12 are U-sha...
PUM
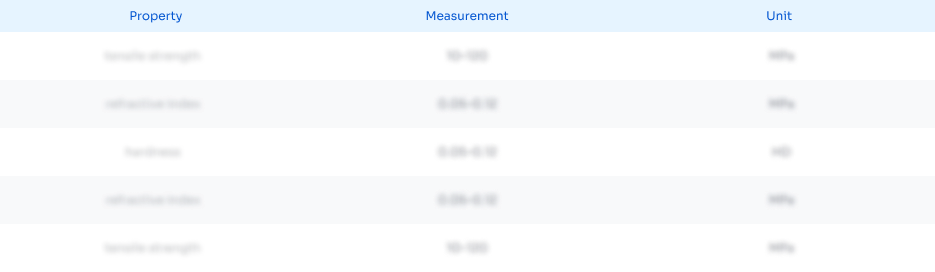
Abstract
Description
Claims
Application Information

- R&D
- Intellectual Property
- Life Sciences
- Materials
- Tech Scout
- Unparalleled Data Quality
- Higher Quality Content
- 60% Fewer Hallucinations
Browse by: Latest US Patents, China's latest patents, Technical Efficacy Thesaurus, Application Domain, Technology Topic, Popular Technical Reports.
© 2025 PatSnap. All rights reserved.Legal|Privacy policy|Modern Slavery Act Transparency Statement|Sitemap|About US| Contact US: help@patsnap.com