Fuel gas mold temperature controller
A technology of mold temperature control and gas, which is applied in the direction of combustion method, combustion control, and fuel supply adjustment, etc. It can solve the problems of poor heat dissipation, insufficient heat exchange, and unfavorable flue gas heat exchange, etc., and achieves convenient control and automatic procedures. high effect
- Summary
- Abstract
- Description
- Claims
- Application Information
AI Technical Summary
Problems solved by technology
Method used
Image
Examples
Embodiment Construction
[0025] exist figure 1 and figure 2 In the gas-fired mold temperature controller shown, a heat-conducting oil furnace 5 is fixedly installed on the frame 6, and a coil is arranged in the combustion chamber 14 of the heat-conducting oil furnace 5, and the coil is separated from the inner wall of the furnace by a spacer - 5.3 , the pitch P of the coil is 2.2 times the diameter d of the pipe, and the coil is formed by connecting the outer coil 5.4 and the inner coil 5.5 coaxially (see image 3 ), the outer coil 5.4 and the inner coil 5.5 are separated by a spacer 5.3, there are two coils, and the two coils are interlaced with each other and connected in parallel (see Figure 4 ), the two oil inlet pipes 5.8 of the two coils are connected in parallel to a general oil inlet pipe, and the oil inlet oil temperature sensor 18.10 and the oil inlet oil pressure gauge 18.11 are installed on the general oil inlet pipe. The two oil outlet pipes 5.7 are connected in parallel to a general ...
PUM
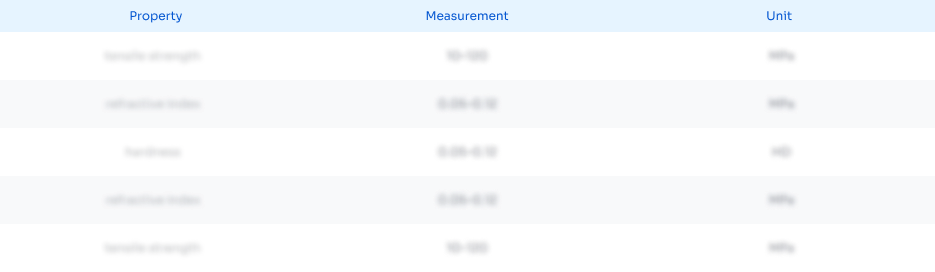
Abstract
Description
Claims
Application Information

- Generate Ideas
- Intellectual Property
- Life Sciences
- Materials
- Tech Scout
- Unparalleled Data Quality
- Higher Quality Content
- 60% Fewer Hallucinations
Browse by: Latest US Patents, China's latest patents, Technical Efficacy Thesaurus, Application Domain, Technology Topic, Popular Technical Reports.
© 2025 PatSnap. All rights reserved.Legal|Privacy policy|Modern Slavery Act Transparency Statement|Sitemap|About US| Contact US: help@patsnap.com