A manufacturing process for a brick for a square
A preparation process, a square brick technology, applied in the field of square bricks, can solve the problems of water accumulation, affect the comfort and safety of the square, increase the drainage burden of the square drainage system, etc., achieve long wear resistance, high strength, color And texture simple and elegant effect
- Summary
- Abstract
- Description
- Claims
- Application Information
AI Technical Summary
Problems solved by technology
Method used
Examples
Embodiment 1
[0018] Embodiment one: choose 36 parts of domestic waste incineration ash, 20 parts of fly ash, 20 parts of blast furnace slag, 12 parts of cement and 12 parts of flux to mix, wherein the domestic waste incineration ash, fly ash and blast furnace slag all need to pass 10 parts. Screening with a sieve above the mesh; Add the obtained mixture to 10% water by mass and stir it evenly in a stirring device, and then let it stand for 2-3 days; Then use the ball making machine to make the above-mentioned aqueous mixture into 1mm particles; select some particles into the press Molding in the machine, adding 1% adhesive by mass during the molding process; then, using the hole opening equipment to punch a number of circular through holes on the bricks, the diameter of the through holes is between 0.5mm-2mm; then, Put the bricks into the kiln for calcination for 5 hours. The calcination temperature in the kiln is controlled between 1100°C and 1300°C. Finally, after the bricks leave the kil...
Embodiment 2
[0019] Embodiment two: choose 40 parts of domestic waste incineration ash, 25 parts of fly ash, 15 parts of blast furnace slag, 10 parts of cement and 10 parts of flux to mix, wherein domestic waste incineration ash, fly ash and blast furnace slag all need to pass 10 parts. Screening with a sieve above the mesh; add water with a mass ratio of 20% to the mixture and then stir it evenly in a stirring device, and then let it stand for 2-3 days; use a ball machine to make the water-containing mixture into 0.5mm particles after standing; select some particles into the press Molding in the machine, adding 3% adhesive by mass during the molding process; then, using the hole opening equipment to punch a number of oval through holes on the bricks, the diameter of the through holes is between 0.5mm-2mm; then, Put the bricks in the fifth step into the kiln for calcination for 8 hours. The calcination temperature in the kiln is controlled between 1100°C and 1300°C. Finally, after the brick...
Embodiment 3
[0020] Embodiment three: choose 50 parts of domestic waste incineration ash, 15 parts of fly ash, 18 parts of blast furnace slag, 7 parts of cement and 10 parts of flux to mix, wherein domestic waste incineration ash, fly ash and blast furnace slag all need to pass 10 parts. Screening with a sieve above the mesh; add water with a mass ratio of 15% to the mixture and then stir it evenly in a stirring device, and then let it stand for 2-3 days; use the ball making machine to make the water-containing mixture obtained in the second step into 1mm particles; select some particles to enter Molding in the press, adding 2% adhesive by mass during the molding process; punching a number of diamond-shaped through-holes on the bricks with the hole-opening equipment, the diameter of the through-holes is between 0.5mm-2mm; then, the blank The bricks are first put into the kiln for calcination for 6 hours, and the calcination temperature in the kiln is controlled between 1100°C and 1300°C; fi...
PUM
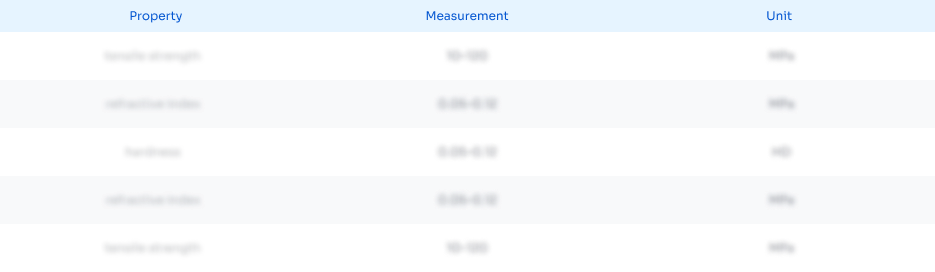
Abstract
Description
Claims
Application Information

- R&D
- Intellectual Property
- Life Sciences
- Materials
- Tech Scout
- Unparalleled Data Quality
- Higher Quality Content
- 60% Fewer Hallucinations
Browse by: Latest US Patents, China's latest patents, Technical Efficacy Thesaurus, Application Domain, Technology Topic, Popular Technical Reports.
© 2025 PatSnap. All rights reserved.Legal|Privacy policy|Modern Slavery Act Transparency Statement|Sitemap|About US| Contact US: help@patsnap.com