Knockout bar connection mechanism of injection molding machine
A technology of connecting mechanism and stripper rod, which is applied in the field of stripping rod connection mechanism, can solve problems such as loose threaded connection, waste of labor and time, mold damage, etc., and achieve the effect of preventing loosening
- Summary
- Abstract
- Description
- Claims
- Application Information
AI Technical Summary
Problems solved by technology
Method used
Image
Examples
Embodiment Construction
[0014] The specific embodiments of the present invention will be further described below in conjunction with the accompanying drawings.
[0015] Such as Figure 1-3 As shown, a stripping rod connection mechanism of an injection molding machine includes a stripping piston rod 1, a stripping plate 3 (also called a ejector plate, used for installing ejector pins), a stripping lever 6, a movable platen 7 and an ejector plate 8 One end of the demoulding rod 6 passes through the movable template 7 and is connected to the ejector plate 8, and the other end of the demolding rod 6 is connected to the demoulding piston rod 1 through the demoulding rod fixing seat 4 , the demoulding rod fixing seat 4 is threadedly connected to the demoulding piston rod 1, and the demoulding rod 6 is formed with an annular groove 61 in the circumferential direction, and a positioning ring is embedded in the annular groove 61 5. The positioning ring 5 is fixedly connected with the demoulding rod fixing se...
PUM
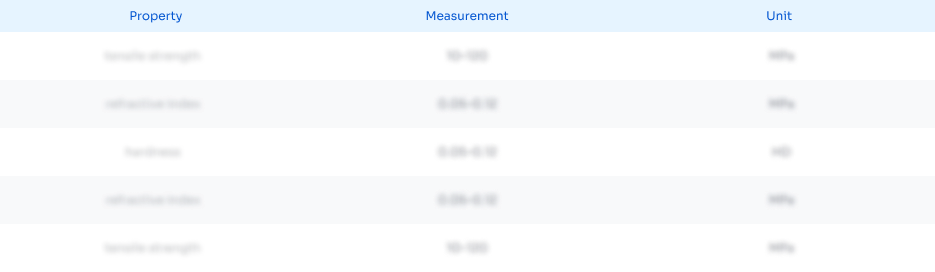
Abstract
Description
Claims
Application Information

- Generate Ideas
- Intellectual Property
- Life Sciences
- Materials
- Tech Scout
- Unparalleled Data Quality
- Higher Quality Content
- 60% Fewer Hallucinations
Browse by: Latest US Patents, China's latest patents, Technical Efficacy Thesaurus, Application Domain, Technology Topic, Popular Technical Reports.
© 2025 PatSnap. All rights reserved.Legal|Privacy policy|Modern Slavery Act Transparency Statement|Sitemap|About US| Contact US: help@patsnap.com