Rotary desulfurization and denitrification reactor and system
A desulfurization and denitrification, rotary technology, applied in chemical instruments and methods, separation methods, gas treatment and other directions, can solve the problems of large amount of waste residue, large area of reaction device, complex system, etc., and achieve high desulfurization rate and denitrification rate. , The effect of improving the destocking efficiency and the high desulfurization and denitrification rate
- Summary
- Abstract
- Description
- Claims
- Application Information
AI Technical Summary
Problems solved by technology
Method used
Image
Examples
Embodiment 1
[0043] Such as figure 1 As shown, a rotary desulfurization and denitrification reactor includes a cylindrical shell 12, a rotating shaft 3 and a partition 11, the rotating shaft 3 is installed inside the cylindrical casing 12, and the partition 11 is fixedly installed on the rotating shaft 3, and the The cylindrical housing 12 is divided into at least two chambers, and the chamber is filled with catalyst, SO 2 The adsorbent 11 is located above the nitrogen oxide catalyst 5, and the rotating shaft 3 rotates under the drive of the motor 13; the top of the cylindrical shell 12 is provided with a flue gas inlet 1 and a reducing gas outlet 4, and the flue gas inlet 1 and the reducing gas outlet 4 Oppositely, the bottom of the cylindrical housing 12 is provided with a flue gas outlet 10 and a reducing gas inlet 9 , the flue gas outlet 10 is located below the flue gas inlet 1 , and the reducing gas inlet 9 is located below the reducing gas outlet 4 . The flue gas inlet 1, the flue g...
Embodiment 2
[0054] A rotary desulfurization and denitrification reactor, comprising a cylindrical shell 12, a rotating shaft 3 and a partition 11, the rotating shaft 3 is installed inside the cylindrical shell 12, the partition 11 is fixedly installed on the rotating shaft 3, and the cylindrical shell 12 separated into at least two chambers filled with catalyst, SO 2 The adsorbent 2 is located above and below the nitrogen oxide catalyst 5, and the rotating shaft 3 rotates under the drive of the motor 13; the bottom of the cylindrical shell 12 is provided with a flue gas inlet 1 and a reducing gas outlet 4, and the flue gas inlet 1 and the reducing gas outlet 4 Oppositely, the top of the cylindrical shell 12 is provided with a flue gas outlet 10 and a reducing gas inlet 9 , the flue gas outlet 10 is located above the flue gas inlet 1 , and the reducing gas inlet 9 is located above the reducing gas outlet 4 .
PUM
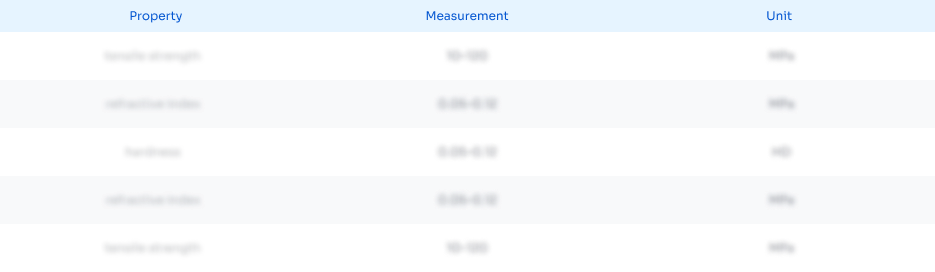
Abstract
Description
Claims
Application Information

- R&D
- Intellectual Property
- Life Sciences
- Materials
- Tech Scout
- Unparalleled Data Quality
- Higher Quality Content
- 60% Fewer Hallucinations
Browse by: Latest US Patents, China's latest patents, Technical Efficacy Thesaurus, Application Domain, Technology Topic, Popular Technical Reports.
© 2025 PatSnap. All rights reserved.Legal|Privacy policy|Modern Slavery Act Transparency Statement|Sitemap|About US| Contact US: help@patsnap.com