Phenol-formaldehyde resin and preparation method thereof
A technology of phenolic resin and bisphenol, applied in the field of phenolic resin and its preparation, can solve the problems of low odor, large residual odor and high formaldehyde content, and achieve the effects of low odor, excellent use environment and low free formaldehyde
- Summary
- Abstract
- Description
- Claims
- Application Information
AI Technical Summary
Problems solved by technology
Method used
Examples
Embodiment 1
[0032] Mix 100g of bisphenol A, 25g of formaldehyde (37% aqueous solution) (bisphenol A:formaldehyde molar ratio 1:0.704) with 10g of water, add 35g of sodium hydroxide, and react at a constant temperature of 120°C for 4 hours under a pressure of 1.0MPa , Get the intermediate;
[0033] Then the intermediate was mixed with 200g glyoxal (40% aqueous solution) (bisphenol A:glyoxal molar ratio 1:3.15), 30g ammonia water (18% aqueous solution) was added, and the pressure was 0.05MPa at 60℃ constant temperature 3 Hours to obtain phenolic resin.
Embodiment 2
[0035] Mix 100g of bisphenol B, 40g of glyoxal (40% aqueous solution) (bisphenol B:glyoxal molar ratio 1:0.67) and 20g of methanol, add 20g of triethylamine, under a pressure of 2.0MPa, 130°C React at a constant temperature for 3 hours to obtain an intermediate;
[0036] Then the intermediate is mixed with 100 g of formaldehyde (37% aqueous solution) (bisphenol B:formaldehyde molar ratio 1:2.99), 20 g of potassium hydroxide is added, and the phenolic resin is obtained at a constant temperature of 60° C. for 3 hours under a pressure of 0.08 MPa.
Embodiment 3
[0038] Mix 100g bisphenol P, 20g furfural (bisphenol P:furfural molar ratio 1:0.72) and 25g ethanol, add 30g sodium hydroxide, 20g triethylamine, and react at 110°C for 2 hours under a pressure of 1.0MPa , Get the intermediate;
[0039] Then the intermediate was mixed with 80 g of formaldehyde (37% aqueous solution) (bisphenol P:formaldehyde molar ratio 1:3.42), and kept at a constant temperature of 50° C. for 4 hours under a pressure of 0.03 MPa to obtain a phenolic resin.
PUM
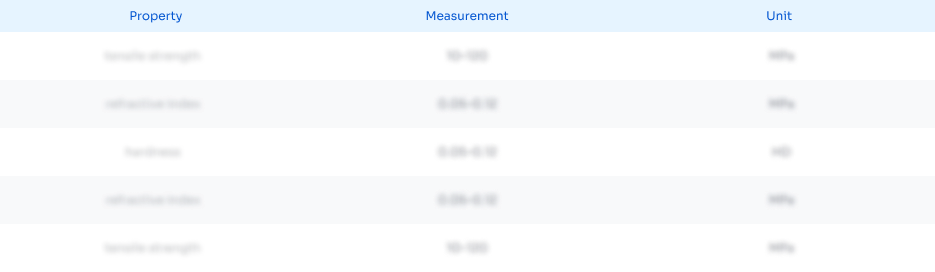
Abstract
Description
Claims
Application Information

- R&D
- Intellectual Property
- Life Sciences
- Materials
- Tech Scout
- Unparalleled Data Quality
- Higher Quality Content
- 60% Fewer Hallucinations
Browse by: Latest US Patents, China's latest patents, Technical Efficacy Thesaurus, Application Domain, Technology Topic, Popular Technical Reports.
© 2025 PatSnap. All rights reserved.Legal|Privacy policy|Modern Slavery Act Transparency Statement|Sitemap|About US| Contact US: help@patsnap.com