Method for phosphorite processing and calcium and magnesium production
A phosphate rock, ammonium sulfate technology, applied in magnesium nitrate, phosphate material processing, calcium/strontium/barium nitrate and other directions, to achieve the effect of increasing the added value of the process, low energy consumption, and improving quality
- Summary
- Abstract
- Description
- Claims
- Application Information
AI Technical Summary
Problems solved by technology
Method used
Examples
Embodiment 1
[0047] A method for processing phosphate rock and producing calcium and magnesium, comprising the following steps:
[0048] (1) Calcining the mined phosphate rock at 1000°C for 1.5h, and then digesting it with 80°C hot water, the amount of hot water is 400ml of water per 1kg of phosphate rock;
[0049] (2) Add 30% ammonium nitrate solution and 50% nitric acid solution to the phosphate rock that has been digested, and stir and leach for 90 minutes at a temperature of 60°C; , the amount of nitric acid solution added is 120g per 1kg of phosphate rock;
[0050] (3) filtering and washing the leached slurry in step 2) to obtain leaching residue and leaching liquid;
[0051] (4) Stir and leach the leach residue with 20% ammonium sulfate solution at a temperature of 80° C. for 90 minutes; filter and wash the leached mixed solution to obtain the filter residue and ammonium sulfate leaching solution; dry the filter residue above 100° C. Dry to obtain high-grade phosphate rock; the dos...
Embodiment 2
[0057] A method for processing phosphate rock and producing calcium and magnesium, comprising the following steps:
[0058] (1) Calcining the mined phosphate rock at 1100° C. for 1.0 h, and then digesting it with hot water at 70° C. The amount of hot water is 500 ml of water per 1 kg of phosphate rock;
[0059] (2) Add 40% ammonium nitrate solution and 60% nitric acid solution to the phosphate rock that has been digested, and stir and leach for 90 minutes at a temperature of 70°C; , the amount of nitric acid solution added is 100g per 1kg of phosphate rock;
[0060] (3) filtering and washing the leached slurry in step 2) to obtain leaching residue and leaching liquid;
[0061] (4) Stir and leach the leach residue with 30% ammonium sulfate solution at a temperature of 75° C. for 60 min; filter and wash the leached mixed solution to obtain the filter residue and ammonium sulfate leach solution; dry the filter residue above 100° C. Dry to obtain high-grade phosphate rock; the d...
Embodiment 3
[0067] A method for processing phosphate rock and producing calcium and magnesium, comprising the following steps:
[0068] (1) Calcining the mined phosphate rock at 1200°C for 0.5h, and then digesting it with hot water at 60°C, the amount of hot water is 600ml of water per 1kg of phosphate rock;
[0069] (2) Add 50% ammonium nitrate solution and 75% nitric acid solution to the phosphate rock that has been digested, and stir and leach for 60 minutes at a temperature of 80°C; , the amount of nitric acid solution added is 110g per 1kg of phosphate rock;
[0070] (3) filtering and washing the leached slurry in step 2) to obtain leaching residue and leaching liquid;
[0071] (4) Stir and leach the leach residue with 20-40% ammonium sulfate solution at a temperature of 70-80° C. for 60-90 min; filter and wash the leached mixed solution to obtain filter residue and ammonium sulfate leaching solution; filter residue Dry above 100°C to obtain high-grade phosphate rock; the dosage of...
PUM
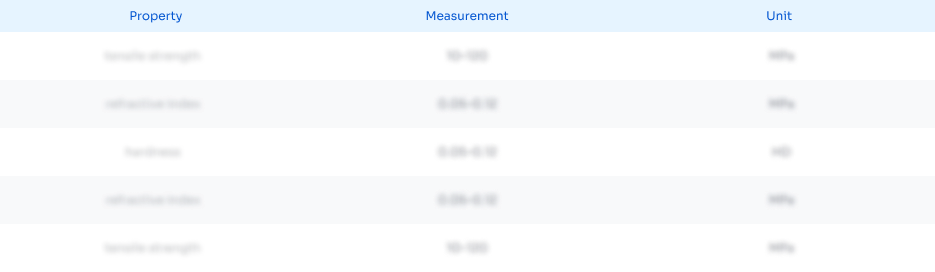
Abstract
Description
Claims
Application Information

- R&D
- Intellectual Property
- Life Sciences
- Materials
- Tech Scout
- Unparalleled Data Quality
- Higher Quality Content
- 60% Fewer Hallucinations
Browse by: Latest US Patents, China's latest patents, Technical Efficacy Thesaurus, Application Domain, Technology Topic, Popular Technical Reports.
© 2025 PatSnap. All rights reserved.Legal|Privacy policy|Modern Slavery Act Transparency Statement|Sitemap|About US| Contact US: help@patsnap.com