Injection molding process method for LED lamp integrally formed through injection molding
A technology of LED lamps and process methods, which is applied to semiconductor devices, lighting devices, light sources and other directions of light-emitting elements, can solve the problem that the production capacity, quality and quality of LED lamps are difficult to guarantee, and the service life and safety of LED lamps are affected. Assembly space and heat dissipation space Large and other problems, to achieve the effect of reducing manufacturing material and labor costs, high yield, and improving heat dissipation efficiency
- Summary
- Abstract
- Description
- Claims
- Application Information
AI Technical Summary
Problems solved by technology
Method used
Image
Examples
Embodiment Construction
[0020] The present invention will be described in further detail below in conjunction with the accompanying drawings.
[0021] The injection molding process method of an integrally molded LED lamp consists of the following steps:
[0022] A) Mount the LED lamp beads on the PCB substrate;
[0023] B) Reserve a cavity for the PCB substrate in step A) on the mold of the injection molding machine, put the PCB substrate mounted with LED lamp beads into the reserved cavity of the mold, and perform integral molding injection molding;
[0024] C) The injection molding method in step B) includes: sequentially injecting glue and melting glue on the PCB substrate in the cavity, and then maintaining the pressure, cooling and then opening the mold, and the cycle of one injection molding is 50-55 seconds.
[0025] In step C), the process of injecting glue and melting glue is divided into six temperature zones successively in the injection molding machine, which are divided into the first t...
PUM
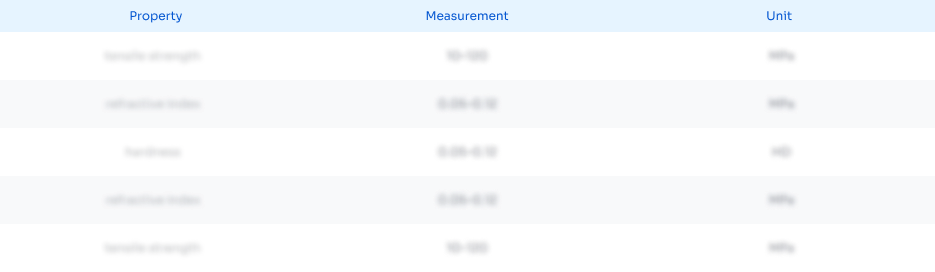
Abstract
Description
Claims
Application Information

- Generate Ideas
- Intellectual Property
- Life Sciences
- Materials
- Tech Scout
- Unparalleled Data Quality
- Higher Quality Content
- 60% Fewer Hallucinations
Browse by: Latest US Patents, China's latest patents, Technical Efficacy Thesaurus, Application Domain, Technology Topic, Popular Technical Reports.
© 2025 PatSnap. All rights reserved.Legal|Privacy policy|Modern Slavery Act Transparency Statement|Sitemap|About US| Contact US: help@patsnap.com