Louvered Rotatable Infrared Heating Cage
A louver-type, infrared heating technology, applied in the direction of ohmic resistance heating, electric heating devices, electrical components, etc., can solve the problems of affecting the cooling rate of spacecraft, blocking the radiation heat exchange between spacecraft and heat sink, prolonging the test time of spacecraft, etc. , to achieve the effect of saving test cost, reducing test time and fully assessing
- Summary
- Abstract
- Description
- Claims
- Application Information
AI Technical Summary
Problems solved by technology
Method used
Image
Examples
Embodiment Construction
[0029] The following is a specific implementation manner of the content of the present invention, and the content of the present invention will be further clarified through the specific implementation mode below. Of course, the following specific embodiments are described only to illustrate different aspects of the present invention, and should not be construed as limiting the scope of the present invention.
[0030] see figure 1 , Figure 1-2 Respectively, a front view and a side view of the louvered infrared cage of the present invention. The rotatable louver-type infrared cage used for the vacuum thermal test process of a spacecraft of the present invention mainly includes an infrared cage main frame 5, a reduction motor 1, a shaft coupling 2, a connecting rod 4 and a pin shaft 11, a heating assembly, a bearing 7 and Bearing seat 6 and angle sensor 12, the side of infrared cage main frame 5 are provided with the motor mount 9 of reduction motor 1, and motor mount and main...
PUM
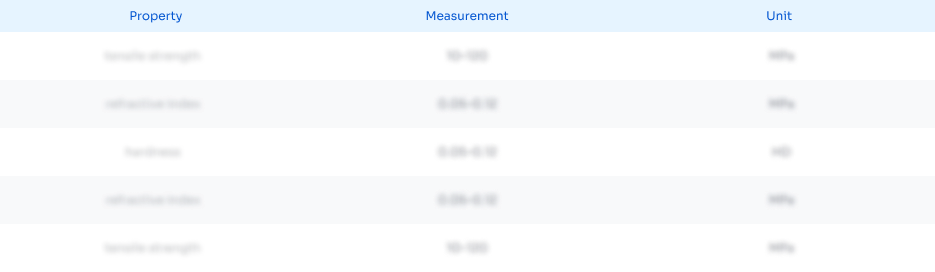
Abstract
Description
Claims
Application Information

- R&D
- Intellectual Property
- Life Sciences
- Materials
- Tech Scout
- Unparalleled Data Quality
- Higher Quality Content
- 60% Fewer Hallucinations
Browse by: Latest US Patents, China's latest patents, Technical Efficacy Thesaurus, Application Domain, Technology Topic, Popular Technical Reports.
© 2025 PatSnap. All rights reserved.Legal|Privacy policy|Modern Slavery Act Transparency Statement|Sitemap|About US| Contact US: help@patsnap.com