High-speed photogravure press
A gravure printing machine, high-speed technology, applied in the direction of gravure rotary printing machine, printing machine, rotary printing machine, etc., can solve the problems of defective or uneven printing, high consumption of air conditioning system, deformation of printing substrate, etc. Good effect, improved overprinting accuracy, consistent speed
- Summary
- Abstract
- Description
- Claims
- Application Information
AI Technical Summary
Problems solved by technology
Method used
Image
Examples
Embodiment
[0029] Refer to attached figure 1 As shown, the high-speed gravure printing machine disclosed in the present invention includes a winding device 11, an unwinding device 1 and at least one set of embossing devices between the rewinding device and the unwinding device, and each group of embossing devices consists of The printing device 4 and the oven heating device 5 are composed of each group of embossing devices connected by transmission guide rollers, and the unwinding traction part 3 connected by transmission guide rollers is installed between the embossing device 4 and the unwinding device, and the embossing device Between the rewinding device and the rewinding device, a rewinding traction section 8 connected by a transmission guide roller is installed, and at least one pendulum roller device 31 for controlling the tension of the printing substrate is arranged on the unwinding traction section 3 and the rewinding traction section 9 , the printing device includes a back pres...
PUM
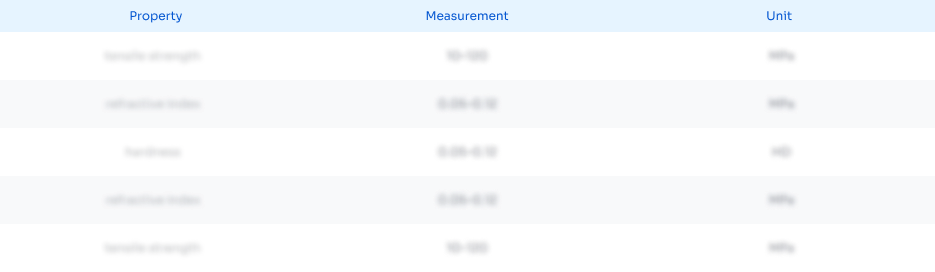
Abstract
Description
Claims
Application Information

- R&D Engineer
- R&D Manager
- IP Professional
- Industry Leading Data Capabilities
- Powerful AI technology
- Patent DNA Extraction
Browse by: Latest US Patents, China's latest patents, Technical Efficacy Thesaurus, Application Domain, Technology Topic, Popular Technical Reports.
© 2024 PatSnap. All rights reserved.Legal|Privacy policy|Modern Slavery Act Transparency Statement|Sitemap|About US| Contact US: help@patsnap.com