Hinge type double-degree-of-freedom modular mechanical arm for EAST device
A robotic arm and hinged technology, applied in the field of hinged dual-degree-of-freedom modular robotic arms, can solve problems such as the difficulty of finding a multi-joint flexible maintenance robotic arm, and does not take into account the harsh operating environment of high temperature and high vacuum, and achieve structural Compactness, the effect of reducing the overall size
- Summary
- Abstract
- Description
- Claims
- Application Information
AI Technical Summary
Problems solved by technology
Method used
Image
Examples
Embodiment Construction
[0033] Such as figure 1shown. A hinged dual-degree-of-freedom modular manipulator for an EAST device, including a U-clamp joint 1, a manipulator barrel 2, a horizontal link 3, a horizontal link 4, a U-clamp joint 5, and a pitch The driver 6, the yaw driver 7 and the yaw drive pulley 8 are composed, the two ends of the double horizontal connecting rods 3 and 4 are hinged with the upper hinge holes of the U-shaped clamp joint 1 and the U-shaped clamp joint 5 respectively, and the pitch driver 6 One end is hinged with the hinge hole of the mechanical arm cylinder 2 and the U-shaped clamp joint 1, the other end of the pitch driver is hinged with the upper hinge hole of the mechanical arm cylinder 2 and the U-shaped clamp joint 5, and the yaw drive 7 is hinged with the mechanical arm One end of the cylinder close to the yaw rotation axis is fixed, and the yaw driving pulley 8 is located on the U-shaped joint joint 5, and is also fixedly connected with the previous joint U-shaped j...
PUM
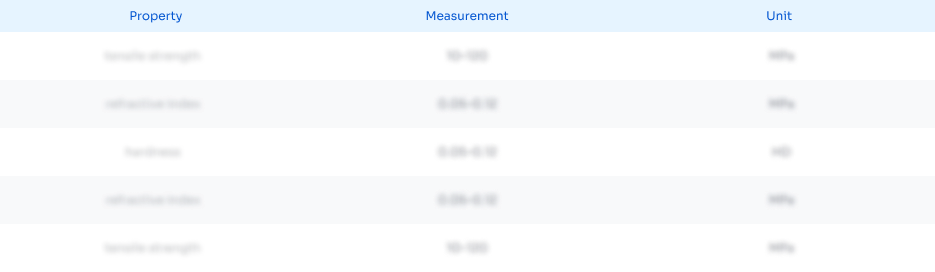
Abstract
Description
Claims
Application Information

- R&D
- Intellectual Property
- Life Sciences
- Materials
- Tech Scout
- Unparalleled Data Quality
- Higher Quality Content
- 60% Fewer Hallucinations
Browse by: Latest US Patents, China's latest patents, Technical Efficacy Thesaurus, Application Domain, Technology Topic, Popular Technical Reports.
© 2025 PatSnap. All rights reserved.Legal|Privacy policy|Modern Slavery Act Transparency Statement|Sitemap|About US| Contact US: help@patsnap.com