Preparation method of flocculant for textile printing and dyeing wastewater decolorization
A decolorizing flocculant, textile printing and dyeing technology, applied in textile industry wastewater treatment, chemical instruments and methods, flocculation / sedimentation water / sewage treatment, etc. and other problems, to achieve high chromaticity and COD removal rate, low temperature storage stability, and the effect of reducing water content
- Summary
- Abstract
- Description
- Claims
- Application Information
AI Technical Summary
Problems solved by technology
Method used
Image
Examples
Embodiment 1
[0013] Embodiment 1, concrete steps are:
[0014] 1) Add 105 kilograms of formaldehyde solution, 66 kilograms of dicyandiamide and 6.42 kilograms of ammonium chloride with a mass concentration of 37% in turn in the enamel kettle A equipped with a reflux condenser and coil heating / cooling, heat to 50 ° C and stir 30 minutes until the solution is transparent;
[0015] 2) Dissolve 15.95 kg of paraformaldehyde in 18.52 kg of NaOH solution with a concentration of 2-4mol / L in reactor B, heat to 60°C and stir to dissolve it;
[0016] 3) Add the solution obtained in step 2) into the enamel kettle A, make the pH of the solution in the enamel kettle A be 7.5±0.2, continue heating to 80°C for 1 hour;
[0017] 4) Add 25.68 kg of ammonium chloride into the enamel kettle A, keep the reaction at 80°C for 3 hours, let it cool down to room temperature after the reaction, and obtain the decolorizing flocculant for textile printing and dyeing wastewater.
Embodiment 2
[0019] 1) Add 125 kg of formaldehyde solution with a mass concentration of 37%, 75.6 kg of dicyandiamide and 8.0 kg of ammonium chloride in sequence in the enamel kettle A equipped with a reflux condenser and coil heating / cooling, heat to 45°C and stir 30 minutes until the solution is transparent;
[0020] 2) Dissolve 20.97 kg of paraformaldehyde in 23.1 kg of NaOH solution with a concentration of 2.5 mol / L in reactor B, heat to 65°C and stir to dissolve it;
[0021] 3) Add the solution obtained in step 2) into the enamel kettle A, so that the pH of the solution in the enamel kettle A is 7.5±0.2, and continue heating to 75° C. for 2 hours;
[0022] 4) Add 32 kg of ammonium chloride into the enamel kettle A, keep it at 75° C. for 2 hours, and let it cool down to room temperature after the reaction, to obtain the decolorizing flocculant for textile printing and dyeing wastewater.
Embodiment 3
[0024] 1) Add 136 kilograms of formaldehyde solution, 80 kilograms of dicyandiamide and 11.4 kilograms of ammonium chloride successively with a mass concentration of 37% in the enamel kettle A equipped with a reflux condenser and coil heating / cooling, heat to 45 ° C and stir 25 minutes until the solution is transparent;
[0025] 2) Dissolve 23.93 kg of paraformaldehyde in 25 kg of NaOH solution with a concentration of 3 mol / L in reactor B, heat to 70°C and stir to dissolve it;
[0026] 3) Add the solution obtained in step 2) into the enamel kettle A, make the pH of the solution in the enamel kettle A be 7.7±0.2, continue heating to 70°C for 2 hours;
[0027] 4) Add 34.2 kg of ammonium chloride into the enamel kettle A, keep the reaction at 70°C for 1 hour, and let it cool down to room temperature after the reaction, to obtain the decolorizing flocculant for textile printing and dyeing wastewater.
PUM
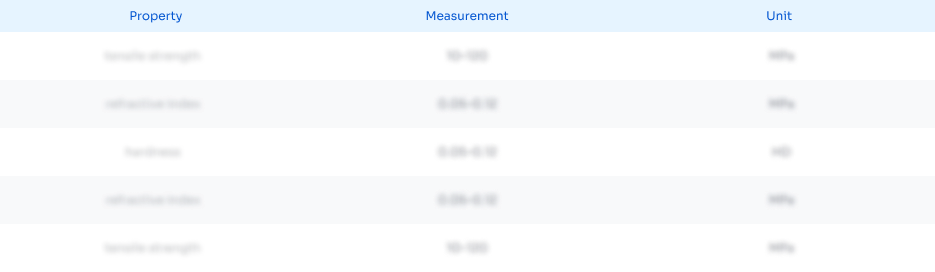
Abstract
Description
Claims
Application Information

- R&D Engineer
- R&D Manager
- IP Professional
- Industry Leading Data Capabilities
- Powerful AI technology
- Patent DNA Extraction
Browse by: Latest US Patents, China's latest patents, Technical Efficacy Thesaurus, Application Domain, Technology Topic.
© 2024 PatSnap. All rights reserved.Legal|Privacy policy|Modern Slavery Act Transparency Statement|Sitemap