PWM self-testing method
A self-detection, square wave signal technology, applied in the direction of measuring electricity, measuring devices, measuring electrical variables, etc., can solve the problems of low filter cut-off frequency, complex processing circuit, and large volume, so as to improve real-time performance and reduce complexity And volume, improve the effect of product quality
- Summary
- Abstract
- Description
- Claims
- Application Information
AI Technical Summary
Problems solved by technology
Method used
Image
Examples
Embodiment Construction
[0015] The present invention will be further described below in conjunction with specific drawings and embodiments.
[0016] In order to effectively improve the real-time performance of PWM detection, reduce the complexity and volume of hardware circuits, and improve the accuracy of PWM detection, the self-test method of the present invention includes the following steps:
[0017] Step 1, collecting the output PWM current signal, and converting the PWM current signal into a square wave signal;
[0018] Specifically, in order to improve the anti-interference ability, the sampling point for collecting the PWM current signal is set in the electronic controller that outputs the PWM current signal, and the PWM current signal is converted into a square wave signal by a hysteresis comparator.
[0019] Generally, the electronic controller includes a CPU for generating PWM signals and a PWM drive circuit, and the PWM drive circuit is connected to the actuator, such as figure 1 shown. ...
PUM
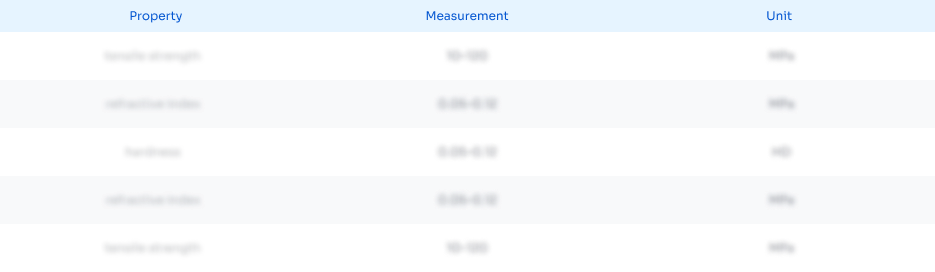
Abstract
Description
Claims
Application Information

- R&D
- Intellectual Property
- Life Sciences
- Materials
- Tech Scout
- Unparalleled Data Quality
- Higher Quality Content
- 60% Fewer Hallucinations
Browse by: Latest US Patents, China's latest patents, Technical Efficacy Thesaurus, Application Domain, Technology Topic, Popular Technical Reports.
© 2025 PatSnap. All rights reserved.Legal|Privacy policy|Modern Slavery Act Transparency Statement|Sitemap|About US| Contact US: help@patsnap.com