Integrated electronic hydraulic servo system
A hydraulic servo system, electric technology, applied in the direction of fluid pressure actuation system components, servo meter circuits, fluid pressure actuation devices, etc., can solve the problems of short working time and inability to start multiple times, to reduce power requirements, reduce Energy consumption and power requirements, the effect of reducing capacity requirements
- Summary
- Abstract
- Description
- Claims
- Application Information
AI Technical Summary
Problems solved by technology
Method used
Image
Examples
Embodiment Construction
[0024] In addition to the embodiments described below, the invention can be embodied in other embodiments or carried out in different ways. It is, therefore, to be understood that the invention is not limited to the details of construction of the components described in the following description or shown in the drawings. While only one embodiment is described here, the claims are not limited to that embodiment.
[0025] Specific embodiments of the present invention will be further described in detail below in conjunction with the accompanying drawings.
[0026] Such as figure 1 as shown,
[0027] An integrated electro-hydraulic servo system, including electro-hydraulic energy, servo actuators, and servo control drivers, is installed in the servo control cabin; the servo battery uses a primary activation thermal battery, including an active thermal battery and a reentry thermal battery; The servo battery receives an activation signal through an electrical connector to provid...
PUM
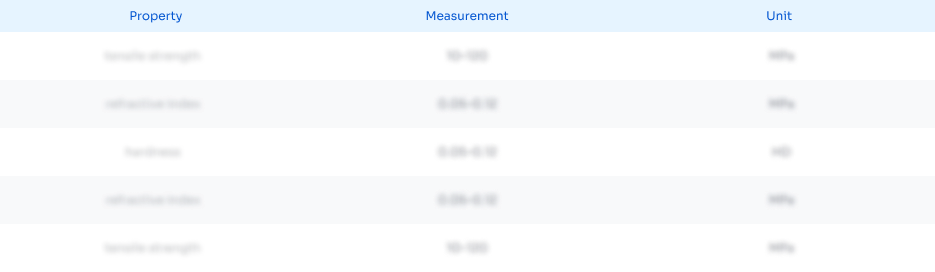
Abstract
Description
Claims
Application Information

- R&D Engineer
- R&D Manager
- IP Professional
- Industry Leading Data Capabilities
- Powerful AI technology
- Patent DNA Extraction
Browse by: Latest US Patents, China's latest patents, Technical Efficacy Thesaurus, Application Domain, Technology Topic, Popular Technical Reports.
© 2024 PatSnap. All rights reserved.Legal|Privacy policy|Modern Slavery Act Transparency Statement|Sitemap|About US| Contact US: help@patsnap.com