A kind of refining method of spring steel
A technology for spring steel and refining slag, applied in the field of spring steel refining, can solve the problems of inability to meet the quality requirements of high-quality spring steel, low basicity and low viscosity of slag series, and achieve low production cost, resource saving and easy control. Effect
- Summary
- Abstract
- Description
- Claims
- Application Information
AI Technical Summary
Problems solved by technology
Method used
Image
Examples
Embodiment 1
[0023] A method for refining spring steel, comprising the steps of
[0024] 1) Converter smelting:
[0025]Using molten iron and steel scrap as raw materials for converter smelting, rapid slag dephosphorization in the early stage of smelting, decarburization and temperature rise in the middle and later stages of smelting, the weight ratio of molten iron and scrap steel added is, molten iron: scrap steel is 5:1, and molten steel and slag are obtained, and then The slag operation is used to tap the converter, and the molten steel flows into the ladle. It is strictly forbidden to flow the oxidized slag in the converter into the ladle; the basicity of the slag is 3.0 when tapping, the FeO content in the slag is 15wt%, and the carbon content in the molten steel is 0.25 wt%, the content of phosphorus is 0.005wt%, the end point temperature of molten steel is: 1640°C; add lime to the ladle after tapping 1 / 3 of the converter, and add silicon-manganese alloy, ferrosilicon and ferrochrom...
Embodiment 2
[0030] A method for refining spring steel, comprising the steps of
[0031] 1) Converter smelting:
[0032] Using molten iron and steel scrap as raw materials for converter smelting, rapid slag dephosphorization in the early stage of smelting, decarburization and heating in the middle and late stages of smelting, the weight ratio of molten iron and scrap steel added is 7:1 for molten iron: scrap steel, and molten steel and slag are obtained, and then The slag operation is used to tap the converter, the molten steel flows into the ladle, and the oxidized slag in the converter is strictly prohibited from flowing into the ladle; the basicity of the slag is 4.0 when tapping, the FeO content in the slag is 18wt%, and the carbon content in the molten steel is 0.20 wt%, the content of phosphorus is 0.004wt%, the end point temperature of molten steel is: 1650°C; add lime to the ladle after tapping 1 / 3 of the converter, and add silicon-manganese alloy, ferrosilicon and ferrochrome at t...
Embodiment 3
[0037] 1) Converter smelting:
[0038] Using molten iron and steel scrap as raw materials for converter smelting, rapid slag dephosphorization in the early stage of smelting, decarburization and temperature rise in the middle and late stages of smelting, the weight ratio of molten iron and scrap steel added is 5.5:1 for molten iron: scrap steel, and molten steel and slag are obtained, and then The slag operation is used to tap the converter, and the molten steel flows into the ladle. It is strictly forbidden to flow the oxidized slag in the converter into the ladle; the basicity of the slag is 3.5 when tapping, the FeO content in the slag is 20wt%, and the carbon content in the molten steel is 0.15 wt%, the content of phosphorus is 0.002wt%, the end point temperature of molten steel is: 1660°C; add lime to the ladle after tapping 1 / 3 of the converter, and add silicon-manganese alloy, ferrosilicon and ferrochrome at the same time to roughly adjust the element composition of molt...
PUM
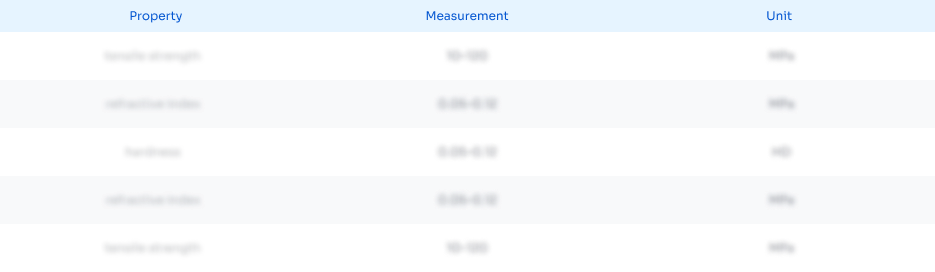
Abstract
Description
Claims
Application Information

- Generate Ideas
- Intellectual Property
- Life Sciences
- Materials
- Tech Scout
- Unparalleled Data Quality
- Higher Quality Content
- 60% Fewer Hallucinations
Browse by: Latest US Patents, China's latest patents, Technical Efficacy Thesaurus, Application Domain, Technology Topic, Popular Technical Reports.
© 2025 PatSnap. All rights reserved.Legal|Privacy policy|Modern Slavery Act Transparency Statement|Sitemap|About US| Contact US: help@patsnap.com