Transformer winding ultrasonic online three-dimensional imaging monitoring method and system
A transformer winding, three-dimensional imaging technology, applied in the direction of using ultrasonic/sonic/infrasonic waves, instruments, measuring devices, etc., can solve the problems of low anti-interference ability, inability to detect online, and difficult to meet the requirements of offline detection methods, and achieve intuitive detection and the effect of the analysis
- Summary
- Abstract
- Description
- Claims
- Application Information
AI Technical Summary
Problems solved by technology
Method used
Image
Examples
Embodiment Construction
[0034] In order to make the above objects, features and advantages of the present invention more comprehensible, specific implementations of the present invention will be described in detail below in conjunction with the accompanying drawings.
[0035] In the following description, numerous specific details are set forth in order to provide a thorough understanding of the present invention. However, the present invention can be implemented in many other ways different from those described here, and those skilled in the art can make similar extensions without violating the connotation of the present invention, so the present invention is not limited by the specific implementations disclosed below.
[0036] The present invention proposes an ultrasonic on-line three-dimensional imaging monitoring method for transformer windings, comprising the following steps:
[0037] S1: Arrange the ultrasonic transmitting probe and receiving probe on the transformer shell, and enter the workin...
PUM
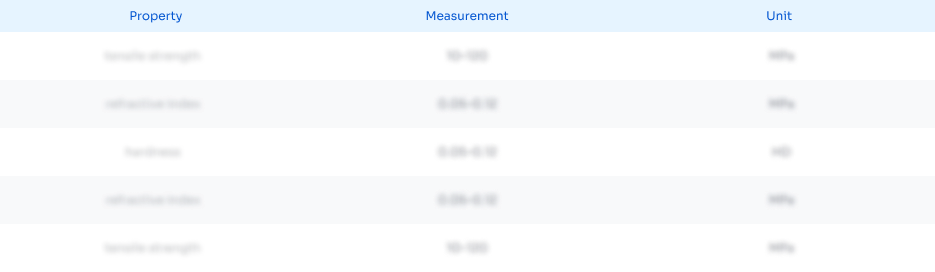
Abstract
Description
Claims
Application Information

- R&D
- Intellectual Property
- Life Sciences
- Materials
- Tech Scout
- Unparalleled Data Quality
- Higher Quality Content
- 60% Fewer Hallucinations
Browse by: Latest US Patents, China's latest patents, Technical Efficacy Thesaurus, Application Domain, Technology Topic, Popular Technical Reports.
© 2025 PatSnap. All rights reserved.Legal|Privacy policy|Modern Slavery Act Transparency Statement|Sitemap|About US| Contact US: help@patsnap.com