Control method and system for shockless shifting of electric drive mechanical transmission without synchronizer
A technology for mechanical transmission and gear shift control, applied in transmission control, mechanical equipment, components with teeth, etc., can solve the problems of high manufacturing and use costs, increased maintenance costs, easy wear and tear of synchronizers, and shorten the power consumption. Interruption time, improved shifting comfort, impact-eliminating impact
- Summary
- Abstract
- Description
- Claims
- Application Information
AI Technical Summary
Problems solved by technology
Method used
Image
Examples
Embodiment Construction
[0036] The present invention will be further described below in conjunction with the accompanying drawings and specific embodiments. It should be emphasized that the following description is only exemplary and not intended to limit the scope of the invention and its application.
[0037] Such as Figure 1-Figure 2 As shown, a non-synchronized electric drive mechanical transmission shockless shift control system includes: a vehicle controller (12), a system coordination controller (8), a dual-target tracking controller (3), a drive motor controller ( 2), a drive motor (1), a rule-based controller (7), a shift controller (6), a shift mechanism (5) and an electrically driven mechanical transmission (4). Among them, the driving motor (1), the electric-driven mechanical transmission (4) and the shifting mechanism (5) all adopt low-cost and high-reliability mature products. The drive motor (1) adopts the drive motor commonly used in electric vehicles at present; the electric drive...
PUM
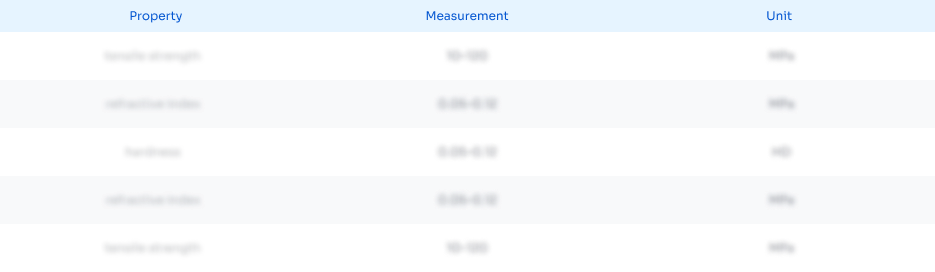
Abstract
Description
Claims
Application Information

- R&D
- Intellectual Property
- Life Sciences
- Materials
- Tech Scout
- Unparalleled Data Quality
- Higher Quality Content
- 60% Fewer Hallucinations
Browse by: Latest US Patents, China's latest patents, Technical Efficacy Thesaurus, Application Domain, Technology Topic, Popular Technical Reports.
© 2025 PatSnap. All rights reserved.Legal|Privacy policy|Modern Slavery Act Transparency Statement|Sitemap|About US| Contact US: help@patsnap.com