A precision forging blade tenon root and front and rear edge processing jig
A technology of front and rear edges and blades, which is applied in the direction of manufacturing tools, metal processing equipment, metal processing machinery parts, etc., can solve the problems of difficult clamping and positioning, poor blank consistency, and easy deformation of blades, so as to improve processing accuracy and efficiency, The clamping force is uniform and the effect of reducing the number of tooling
- Summary
- Abstract
- Description
- Claims
- Application Information
AI Technical Summary
Problems solved by technology
Method used
Image
Examples
Embodiment Construction
[0023] This embodiment is a precision forging blade tenon and a processing fixture for the front and rear edges.
[0024] see Figure 1 to Figure 7 In this embodiment, the precision forging blade tenon and the front and rear edge processing fixtures are composed of a pouring box cover 1, a pouring box seat 2, a turntable 3, a support arm 4, a pressure rod 5, a pressure plate 6, a first rotating shaft 7, and a second rotating shaft 8 , Compression bolts 9, bolts 10, tightening bolts 11, first positioning pin 12, second positioning pin 13, third positioning pin 14, the rotary table 3 is connected with the rotary shaft of the machine tool, and the rotary table 3 is used to support other components. The support arm 4 is located on the turntable 3, the upper part of the support arm 4 has two lugs with shaft holes, the bottom of the support arm 4 is provided with two positioning blind holes and two threaded blind holes, and the corresponding parts of the turntable 3 are provided wit...
PUM
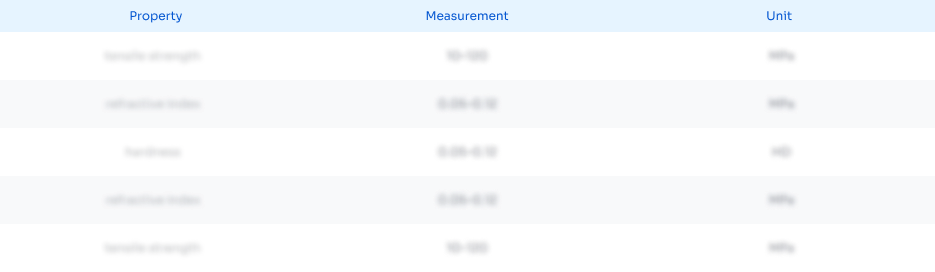
Abstract
Description
Claims
Application Information

- Generate Ideas
- Intellectual Property
- Life Sciences
- Materials
- Tech Scout
- Unparalleled Data Quality
- Higher Quality Content
- 60% Fewer Hallucinations
Browse by: Latest US Patents, China's latest patents, Technical Efficacy Thesaurus, Application Domain, Technology Topic, Popular Technical Reports.
© 2025 PatSnap. All rights reserved.Legal|Privacy policy|Modern Slavery Act Transparency Statement|Sitemap|About US| Contact US: help@patsnap.com