Self-circulation gas-liquid two-phase flow phase change heat exchanger
A phase change heat exchanger, gas-liquid two-phase flow technology, applied in indirect heat exchangers, lighting and heating equipment, etc., can solve the influence of the working performance of heat pipe heat exchangers and limit the heat transfer capacity of heat pipe heat exchangers and other problems, to achieve the effect of enhancing condensation heat transfer capacity, reducing mutual influence and smooth working fluid circulation
- Summary
- Abstract
- Description
- Claims
- Application Information
AI Technical Summary
Problems solved by technology
Method used
Image
Examples
Embodiment Construction
[0034] A further detailed description is carried out below in conjunction with the description of the accompanying drawings:
[0035] figure 1 Shown is a schematic diagram of the three-dimensional structure of a self-circulating gas-liquid two-phase flow phase-change heat exchanger working under anti-gravity conditions. It is a closed heat exchanger composed of an evaporation plate 1, a condensation plate 2, an annular wall surface 3 and a capillary cavity. The capillary cavity is composed of a liquid-absorbing core 4 and a gas-liquid two-phase working fluid. The evaporating plate 1 and the condensing plate 2 are connected by an annular wall 3; the liquid-absorbing core 4 is a gradient liquid-absorbing core rolled from wire mesh with different apertures, and the gradient liquid-absorbing core is covered with capillary chambers; the evaporating plate 1 is equipped with The groove 5, the groove 5 is a stepped bifurcated groove extending radially outward from the center. In add...
PUM
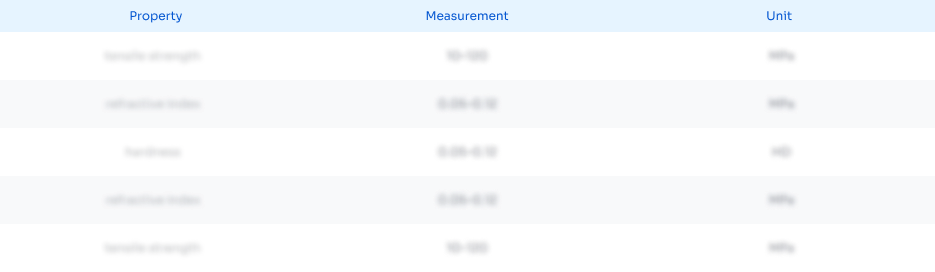
Abstract
Description
Claims
Application Information

- R&D
- Intellectual Property
- Life Sciences
- Materials
- Tech Scout
- Unparalleled Data Quality
- Higher Quality Content
- 60% Fewer Hallucinations
Browse by: Latest US Patents, China's latest patents, Technical Efficacy Thesaurus, Application Domain, Technology Topic, Popular Technical Reports.
© 2025 PatSnap. All rights reserved.Legal|Privacy policy|Modern Slavery Act Transparency Statement|Sitemap|About US| Contact US: help@patsnap.com