Defect detection method and system based on visual recognition
A defect detection and visual recognition technology, which is applied in image analysis, image enhancement, instruments, etc., can solve the problems of not being able to prevent bad batches in advance, increase production costs, and damage to printing screens, so as to avoid bad batches of products and improve efficiency. Production capacity, the effect of reducing the requirements of testing conditions
- Summary
- Abstract
- Description
- Claims
- Application Information
AI Technical Summary
Problems solved by technology
Method used
Image
Examples
Embodiment Construction
[0038] In order to make the object, technical solution and advantages of the present invention clearer, various embodiments of the present invention will be described in detail below in conjunction with the accompanying drawings. However, those of ordinary skill in the art can understand that, in each implementation manner of the present invention, many technical details are provided for readers to better understand the present application. However, even without these technical details and various changes and modifications based on the following implementation modes, the technical solution claimed in this application can also be realized.
[0039] The first embodiment of the present invention relates to a defect detection method based on visual recognition. The specific process is as Figure 9 shown.
[0040] Step 301: Get an image.
[0041] Specifically, an image of the panel to be inspected is acquired. In the acquisition process, connect the camera to acquire the image, c...
PUM
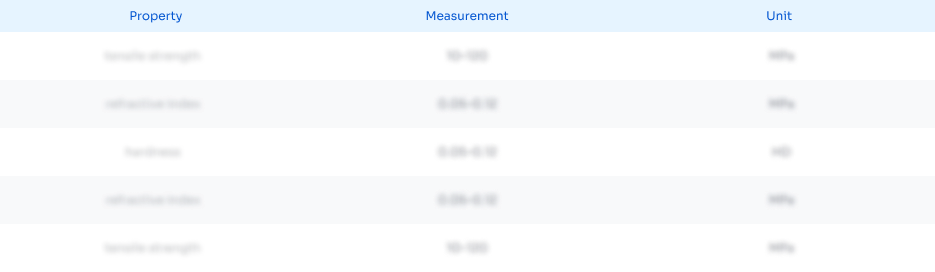
Abstract
Description
Claims
Application Information

- R&D
- Intellectual Property
- Life Sciences
- Materials
- Tech Scout
- Unparalleled Data Quality
- Higher Quality Content
- 60% Fewer Hallucinations
Browse by: Latest US Patents, China's latest patents, Technical Efficacy Thesaurus, Application Domain, Technology Topic, Popular Technical Reports.
© 2025 PatSnap. All rights reserved.Legal|Privacy policy|Modern Slavery Act Transparency Statement|Sitemap|About US| Contact US: help@patsnap.com