Novel self-thermal-insulation sintered bricks containing building wastes and production method of novel self-thermal-insulation sintered bricks
A construction waste and self-insulation technology, which is applied to clay products, other household appliances, household appliances, etc., can solve the problems of waste of resources, destruction of the natural environment, land waste, etc., and achieve the effect of low cost, good insulation effect and stable performance
- Summary
- Abstract
- Description
- Claims
- Application Information
AI Technical Summary
Problems solved by technology
Method used
Examples
Embodiment 1
[0022] 28-40 parts of construction waste, 37-50 parts of engineering dregs, and 28-40 parts of cinder.
[0023] Preparation:
[0024] Dry or sun-dry the construction waste, engineering dregs and cinders until the moisture content is 8%, 13% and 9%, respectively, and then put the construction waste and cinders into a pulverizer for crushing to obtain particle sizes of 1dmm-3mm respectively , 1dmm ~ 3mm construction waste powder, cinder powder, and engineering slag are processed; then the obtained construction waste powder, engineering slag, and cinder powder are put in a mixer in proportion to stir to obtain a mixture; then the mixture After aging for 5 days, an aged mixture with a moisture content of 15% is obtained; then the aged mixture is transported to the mixer, and then enters the extruder to form strips, cut into bricks, and the cut bricks are stacked by an automatic stacking machine When the kiln car in the tunnel kiln enters the tunnel kiln, it is roasted at a temper...
Embodiment 2
[0026] 20-40 parts of construction waste, 40-65 parts of engineering dregs, and 30-45 parts of cinder.
[0027] Preparation:
[0028] Dry or sun-dry the construction waste, engineering dregs and cinders until the moisture content is 5%, 16% and 8%, respectively, and then put the construction waste and cinders into a pulverizer for crushing to obtain particle sizes of 1dmm-3mm respectively , 1dmm ~ 3mm construction waste powder, cinder powder, and engineering slag are processed; then the obtained construction waste powder, engineering slag, and cinder powder are put in a mixer in proportion to stir to obtain a mixture; then the mixture After aging for 3 days, an aged mixture with a moisture content of 14% is obtained; then the aged mixture is transported to the mixer, and then enters the extruder to form strips, cut into bricks, and the cut bricks are stacked by an automatic stacking machine When the kiln car in the tunnel kiln enters the tunnel kiln, it is roasted at a temper...
Embodiment 3
[0030] 38-50 parts of construction waste, 30-45 parts of engineering dregs, and 23-40 parts of cinder.
[0031] Preparation:
[0032] Dry or sun-dry the construction waste, engineering dregs and cinders until the moisture content is 8%, 16% and 10%, respectively, and then put the construction waste and cinders into the pulverizer for crushing, and obtain particle sizes of 1dmm-3mm respectively , 1dmm ~ 3mm construction waste powder, cinder powder, and engineering slag are processed; then the obtained construction waste powder, engineering slag powder, and cinder powder are put together in a mixer for stirring to obtain a mixture; then the mixture is aged After curing for 7 days, an aged mixture with a moisture content of 17% was obtained; after that, the aged mixture was transported to a mixer, and then entered into an extruder to form strips, then cut into bricks, and the cut bricks were stacked by an automatic stacking machine The kiln car of the tunnel kiln enters the tunn...
PUM
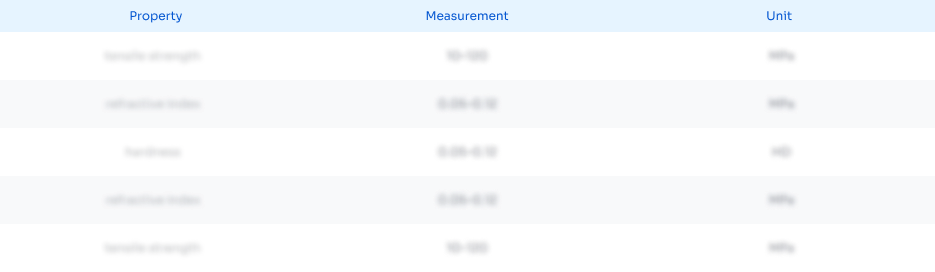
Abstract
Description
Claims
Application Information

- R&D Engineer
- R&D Manager
- IP Professional
- Industry Leading Data Capabilities
- Powerful AI technology
- Patent DNA Extraction
Browse by: Latest US Patents, China's latest patents, Technical Efficacy Thesaurus, Application Domain, Technology Topic, Popular Technical Reports.
© 2024 PatSnap. All rights reserved.Legal|Privacy policy|Modern Slavery Act Transparency Statement|Sitemap|About US| Contact US: help@patsnap.com