Coating for electric iron and its preparation and application method
A technology for electric irons and coatings, applied in the direction of fireproof coatings, epoxy resin coatings, coatings, etc., can solve the problems of easy paint falling off, not resistant to scratches and wear, insufficient hardness, etc., and achieve smooth surface, excellent heat and humidity resistance, and production short duration effect
- Summary
- Abstract
- Description
- Claims
- Application Information
AI Technical Summary
Problems solved by technology
Method used
Image
Examples
preparation example Construction
[0029] Correspondingly, on the basis of providing the formulation of the paint for electric iron, the embodiment of the present invention also provides a preparation method of the paint for electric iron. In an embodiment, the preparation method of the coating for an electric iron at least includes the following steps: weighing acrylic resin, amino resin, epoxy resin, sealed curing agent, toner, auxiliary agent (auxiliary agent includes Dispersants, anti-settling agents, leveling agents, adhesion promoters) and organic solvents;
[0030] Mixing the weighed organic solvent, acrylic resin, dispersant, anti-sedimentation agent, and toner to obtain the first material;
[0031] Grinding the first material;
[0032] adding the amino resin, closed curing agent, and epoxy resin to the first material in sequence, and performing mixing treatment to obtain a second material;
[0033] Add the leveling agent and the adhesion promoter into the second material, and adjust the viscosity.
...
Embodiment 1~3
[0041] In order to save space, the weight percentages of the raw material formulations of Examples 1 to 3 are listed in Table 1, specifically as follows.
[0042] Table 1 embodiment 1~3 each formula component weight percent (unit: %)
[0043]
[0044]
[0045] The preparation process of above-mentioned each embodiment coating is:
[0046] The first material is obtained by first mixing part of the organic solvent with the acrylic resin, dispersant, anti-sedimentation agent, and toner;
[0047] Grinding the first material so that the particles of the first material are 10 microns or less;
[0048] adding amino resin, closed curing agent, and epoxy resin to the ground first material, and mixing to obtain the second material;
[0049] Add the leveling agent and the adhesion promoter into the second material, and use the remaining organic solvent to adjust the viscosity of the paint to obtain the paint for electric irons in various embodiments.
PUM
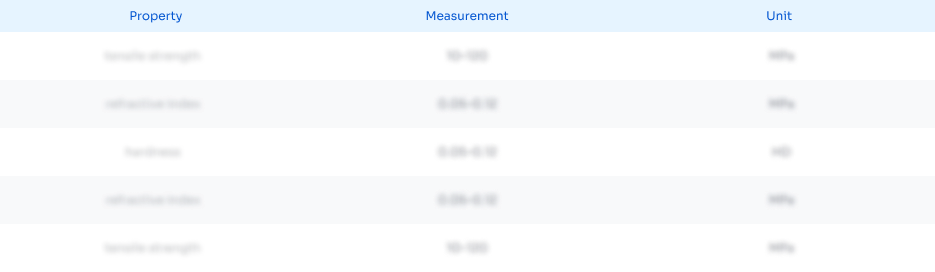
Abstract
Description
Claims
Application Information

- R&D
- Intellectual Property
- Life Sciences
- Materials
- Tech Scout
- Unparalleled Data Quality
- Higher Quality Content
- 60% Fewer Hallucinations
Browse by: Latest US Patents, China's latest patents, Technical Efficacy Thesaurus, Application Domain, Technology Topic, Popular Technical Reports.
© 2025 PatSnap. All rights reserved.Legal|Privacy policy|Modern Slavery Act Transparency Statement|Sitemap|About US| Contact US: help@patsnap.com